Waters 432 conductivity detector operator's guide
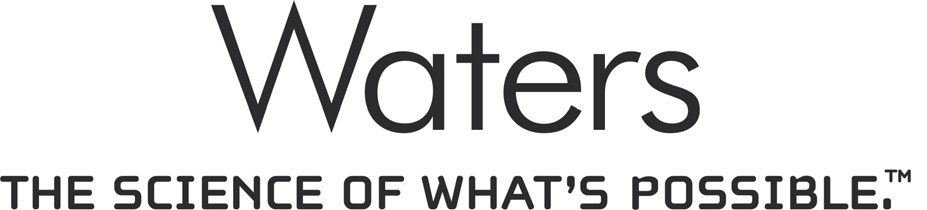
Waters 432 Conductivity
Copyright Waters Corporation 2010
All rights reserved
2010 WATERS CORPORATION. PRINTED IN THE UNITED STATES OF
AMERICA AND IN IRELAND. ALL RIGHTS RESERVED. THIS
DOCUMENT OR PARTS THEREOF MAY NOT BE REPRODUCED IN ANY
FORM WITHOUT THE WRITTEN PERMISSION OF THE PUBLISHER.
The information in this document is subject to change without notice and
should not be construed as a commitment by Waters Corporation. Waters
Corporation assumes no responsibility for any errors that may appear in this
document. This document is believed to be complete and accurate at the time
of publication. In no event shall Waters Corporation be liable for incidental or
consequential damages in connection with, or arising from, its use.
Alliance, Millennium, and Waters are registered trademarks of Waters
Corporation, and Empower, LAC/E, PowerLine, SAT/IN, Sep-Pak,
UltraWISP, WISP and "THE SCIENCE OF WHAT'S POSSIBLE." are
trademarks of Waters Corporation.
Other registered trademarks or trademarks are the sole property of their
Waters' Technical Communications department invites you to tell us of any
errors you encounter in this document or to suggest ideas for otherwise
improving it. Please help us better understand what you expect from our
documentation so that we can continuously improve its accuracy and
usability.
We seriously consider every customer comment we receive. You can reach us
Contact Waters® with enhancement requests or technical questions regarding
the use, transportation, removal, or disposal of any Waters product. You can
reach us via the Internet, telephone, or conventional mail.
Waters contact information
The Waters Web site includes contact
information for Waters locations worldwide.
Telephone and fax
From the USA or Canada, phone 800
252-HPLC, or fax 508 872 1990.
For other locations worldwide, phone and fax
numbers appear in the Waters Web site.
Conventional mail
Waters Corporation34 Maple StreetMilford, MA 01757USA
Some reagents and samples used with Waters instruments and devices can
pose chemical, biological, and radiological hazards. You must know the
potentially hazardous effects of all substances you work with. Always follow
Good Laboratory Practice, and consult your organization's safety
representative for guidance.
for a comprehensive list of warning and caution
Operating this instrument
When operating this instrument, follow standard quality-control (QC)
procedures and the guidelines presented in this section.
Manufacturer location
Authorized representative of the European
Confirms that a manufactured product complies
with all applicable European Community
Australia C-Tick EMC Compliant
Confirms that a manufactured product complies
with all applicable United States and Canadian
safety requirements
Consult instructions for use
Audience and purpose
This guide is intended for personnel who install, operate, and maintain the
Waters 432 Conductivity Detector.
Intended use of the Waters 432 Conductivity Detector
Use the Waters® 432 Conductivity Detector, as a standalone module or
configured as part of an HPLC system, to determine changes in the thermal
conductivity of column eluent as compared with that from a reference flow.
The Waters 432 Conductivity Detector is for research use only.
To calibrate LC systems, follow acceptable calibration methods using at least
five standards to generate a standard curve. The concentration range for
standards should include the entire range of QC samples, typical specimens,
and atypical specimens.
When calibrating mass spectrometers, consult the calibration section of the
operator's guide for the instrument you are calibrating. In cases where an
overview and maintenance guide, not operator's guide, accompanies the
instrument, consult the instrument's online Help system for calibration
Routinely run three QC samples that represent subnormal, normal, and
above-normal levels of a compound. Ensure that QC sample results fall within
an acceptable range, and evaluate precision from day to day and run to run.
Data collected when QC samples are out of range might not be valid. Do not
report these data until you are certain that the instrument performs
ISM Classification: ISM Group 1 Class B
This classification has been assigned in accordance with CISPR 11 Industrial
Scientific and Medical (ISM) instruments requirements. Group 1 products
apply to intentionally generated and/or used conductively coupled
radio-frequency energy that is necessary for the internal functioning of the
equipment. Class B products are suitable for use in both commercial and
residential locations and can be directly connected to a low voltage,
EC authorized representative
Waters Corporation (Micromass UK Ltd.)Floats RoadWythenshaweManchester M23 9LZUnited Kingdom
Table of Contents
Table of Contents
connections . 2-13
Table of Contents
Table of Contents
Table of Contents
Table of Contents
Table of Contents
The Waters® 432 Conductivity Detector is specifically designed to be
integrated into chromatographic systems. The following features contribute to
its performance in measuring the conductivity of column eluents:
Unique 5-electrode flow cell design
Heat exchanger and a built-in automatic temperature control system for
Auto baseline/auto zero
External recorder/integrator and chart mark connections
Three time constant selections
"Leak-detected" alarm signal
Waters 432 conductivity detector
Conductivity Detector
Method of operation
This section discusses the method of operation of the 432 Detector. Additional
descriptive information appears in these sections:
The 432 Detector responds to all ions present in the flow cell, since all ions in
solution conduct electricity. This allows the 432 Detector to detect a wide
variety of sample ions.
The 432 Detector eliminates the eluent's contribution to conductivity with an
electronic technique called baseline suppression. The detector measures the
eluent conductivity and assigns it a value of zero. Thus, any sample ions
appear as positive or negative measurements, relative to the baseline.
The temperature of an ionic solution affects the conductivity of the ions.
Generally, a solution's conductivity rises about 2% for every degree Celsius of
temperature increase. The special flow cell heater in the 432 Detector
minimizes the effect of ambient temperature fluctuations on measurement
Flow cell design
The flow cell in the 432 Detector contains five electrodes connected in a
measuring circuit: two reference electrodes, two detection electrodes, and a
guard electrode that provides a local electrical "ground". Column eluent flows
through the heater to attain the set temperature, and then flows through the
cell, directly contacting the electrodes. The 5-electrode design permits
measurement of conductivity to be made with a very low current at the
detection electrodes. The low current employed eliminates impedance and
other problems associated with simpler designs, and results in a stable
baseline and an extended range of linearity.
Method of operation
Flow cell schematic
1=Reference electrodes
1= Reference Electrodes
2=Detection electrodes
2= Detection Electrodes
3=Guard electrode
3= Guard Electrode
Flow cell block ck
Ion detection theory
The conductance of a solution of known concentration can be calculated using
the following equation:
G = measured conductance of the solution, in Siemens (1 S = ohm−1)
C = concentration in equivalents per 1000 cm3K = length/area of cell (the cell constant)
λ = equivalent conductance in S cm2 equiv−1
The table below lists the equivalent conductances of some common ions.1 Concentrations above 10-5 to 10-3 N, generally exhibit decreased equivalent
conductance due to interionic effects.
Limiting equivalent conductance of ions in water at 25 °C
1. Henry H. Bauer et al., eds. "Instrumental Analysis," Allyn and Bacon, Boston (1978), p. 115. Reprinted
with permission from the publisher.
Ion detection theory
2 Installing the Detector
This chapter guides you through the following steps in preparing the 432
Detector for operation in a chromatographic system:•
Selecting an installation site that satisfies the detector's power and
Unpacking and inspecting the 432 Detector and accompanying
Connecting the detector to your AC power supply
Connecting the detector electrically to the other components of your
chromatographic system
Connecting the detector inlet to the column and the detector outlet
to a waste receptacle (and, if required, installing the pulse
Passivating the detector and other post-column fluid path
After you have successfully completed this chapter, familiarize yourself
are ready to operate the detector, perform the startup procedure
described in Contents
Selecting the installation site
The 432 Detector operates in any standard laboratory environment that
provides suitable electrical power and remains within the following ranges:
Temperature: 5 to 35 °C (40 to 95 °F)
Humidity: 20 to 80%, noncondensing
Install the instrument in a clean area that is free from exposure to:
Temperature or humidity extremes, which can be found near direct
sunlight, heat registers, and air conditioning vents
Strong electromagnetic radiation, such as from large motors or arcing
Appreciable shock or vibration
The 432 Detector requires bench space that measures approximately:
10 inches (25 cm) high
14 inches (34 cm) wide
24 inches (60 cm) deep
Caution: Make sure that air can circulate freely through the ventilation
slots on both side panels.
The 432 Detector requires:
One properly grounded AC voltage outlet.
Correct voltage and fuse selections as shown in the
Installing the Detector
Unpacking and inspection
The 432 Detector is shipped in one carton that contains the following items:
Waters 432 Conductivity Detector
Validation certificate
Waters 432 Conductivity Detector Operator's Guide
Declaration of conformity
Tip: If you purchased the 432 Detector as part of an ion/liquid chromatograph
system, a Waters representative will perform the installation and startup.
To unpack the 432 Detector:
1. Locate the packing list.
2. Unpack the contents of the shipping carton and check the contents
against the packing list to make sure that you received all items.
3. Check the contents of the Startup Kit against the Waters 432
Conductivity Detector Startup Kit List.
4. Save the shipping carton for future transport or shipment.
Inspect all items. If you find any damage or discrepancy, immediately contact
the shipping agent and Waters. For more information about the instrument
warranty, refer to Waters Licenses, Warranties, and Support.
If the shipment is complete and undamaged, record the installation date and
serial number of the 432 Detector in the spaces provided in
Unpacking and inspection
AC power connection
Warning: To avoid a potential fire hazard and damage to the 432
Detector, make sure that the voltage selector in the power connector is
set correctly to match the available AC power source, and that the
correct fuses are installed before you apply AC power.
Power cord
The power connector is located on the lower-right corner of the rear panel. If a
power plug other than the one supplied is needed for your location, consult the
existing applicable regulations.
Installing the Detector
Rear panel
IEEE DIPswitch cover
Power cord wire identification
Wire (USA)
The 432 Detector can be adapted to operate within two voltage ranges at 50 or
60 Hz. The table below describes these voltage ranges and the fuse value that
is appropriate to each.
AC power connection
Nominal operating voltage
Nominal Voltage (VAC) Fuse
100/120
You need a flat-blade screwdriver to perform this procedure.
Warning: To avoid the possibility of electrical shock, turn off the front
panel power switch and unplug the power cord.
To change the operating voltage setting:
1. Remove the power cord from its connector on the rear panel of the
controller and pry open the power connector cover with a flat-blade
2. Remove the voltage selection barrel and locate the correct voltage
3. Reinstall the voltage selection barrel so the desired voltage setting
appears through the window when you close the power connector cover.
Installing the Detector
Changing the voltage setting
4. Determine if you need to change the fuses (s
). All units are supplied with two 2-A fuses
installed for 100/120 volt operation. If you operate the unit on 220/240
volt power, change the fuse as outlined in
5. Reinstall the power connector cover and the power cord.
I/O signal connections
The 432 Detector is usually installed as an integral part of a data collection
system. You can control the 432 Detector either locally from the keypad on the
front panel or remotely from a PowerLine™ controller, such as the Waters
600S.
This section describes the detector's I/O signals and how they connect to the
following devices:
PowerLine controller
Empower™ or Millennium®32 software
SAT/IN ™ module
I/O signal connections
Device signalling the Chart Marker input
Device signalling the Auto Zero input
Caution: To meet the regulatory requirements of immunity from
external electrical disturbances that may affect the performance of this
instrument, do not use cables longer than 9.8 feet (3 meters) when
connecting to the screw-type barrier terminal strips. In addition, ensure
you always connect the shield of the cable to chassis ground at one
instrument only.
I/O signal descriptions
The 432 Detector rear panel has an IEEE-488 connector for communication
with a PowerLine controller, and a terminal strip for the input/output signals.
Installing the Detector
I/O terminal strip
I/O signal descriptions
Recorder output – A 10-mV full-scale analog output
signal appears on these terminals. The measurement
range is determined by the product of the Base Range
and Sensitivity settings: for example, 500 μS (base
range) x 0.005 (sensitivity) = 2.5 μS full scale.
Integrator output – A 1-V full-scale analog output
signal appears on these terminals. The measurement
range is selectable:
10, 50, or 100 μS full scale.
Marker output – A 1-second contact closure signal
appears on these terminals when either of the
following events occurs:• The Chart Mark key on the keypad is pressed• A contact closure signal occurs between the
Marker In terminals
I/O signal connections
I/O signal descriptions (Continued)
Leak Alert output – A contact closure signal
appears on these terminals if a leak is detected inside
the detector.
Auto Zero input – The voltage at the Recorder and
Integrator output terminals is set to the user-selected
balance offset level when a contact closure occurs
between these terminals.
Marker input – A chart mark ( 0.5 mV for 3
seconds) is added to the Recorder output signal when
a contact closure signal appears between these
To connect cables to the I/O terminals, use a small flat-blade screwdriver.
Other rear panel connections and DIP switch
In addition to the I/O terminal strip, the rear panel also contains the following
IEEE-488 connector – Communication bus for use with a Waters
PowerLine system controller, such as the Waters 600S.
DIP switch – Sets the IEEE-488 address seen by the system controller.
Ground lugs – Used to connect the 432 Detector to an earth ground
connection and also used as a chassis ground connection to other system
PowerLine controller connections
The 432 Detector can be programmed remotely by a PowerLine controller
(such as the Waters 600S) via the IEEE-488 data communications bus.
You need a 2.5-mm Allen wrench to connect to the 432 Detector.
Installing the Detector
To connect the 432 Detector to a PowerLine controller:
1. Turn off the PowerLine controller and the 432 Detector.
2. Plug one end of the IEEE-488 cable (included in the Startup Kit) into the
bus connector on the rear panel of the 432 Detector (see th
e other end of the cable into the bus connector
on the PowerLine controller.
3. Remove the DIP switch cover (see th
using a 2.5-mm Allen wrench.
4. Refer to the to
set the DIP switches on the rear panel of the 432 Detector (see the
ue IEEE-488 address
between 2 and 29.
5. After you set the DIP switches, reinstall the DIP switch cover.
Tip: To operate the 432 Detector in local mode, press the front panel Remote
key. The illuminated light above the key will go out.
IEEE-488 address switch
(Address 8 Shown)
I/O signal connections
The IEEE-488 address DIP switch employs positive logic to determine the
address of the 432 Detector from the switch settings. The table below shows
the settings for valid addresses.
IEEE-488 DIP switch setting
IEEE-488
DIP switch settings
Installing the Detector
IEEE-488 DIP switch setting (Continued)
IEEE-488
DIP switch settings
Under PowerLine control, the 432 Detector is recognized as a 431 Detector
and it retains the functionality of the 431 Detector with the following
The Balance field on the detector setup page of the PowerLine controller
affects the Integrator Balance and the Integrator Output only.
When you press the Setup key on the controller, the selected Balance
value is sent to the 432 Detector from the PowerLine controller.
However, the 432 Detector output does not change to the selected
balance until the detector is autozeroed by a contact closure at the Auto
Zero input terminals on the rear panel (remote or local mode) or when
you press the Auto Zero key on the front panel (local mode only).
Under PowerLine control, the 432 Detector retains the full functionality of
local mode operation, except for the following differences:
The Recorder Sensitivity ranges of 0.0002 and 0.0001 are not accessible.
The Integrator Sensitivity ranges are not accessible.
The 432 Detector does not automatically perform an Auto Zero after an
Auto Base routine has occurred.
Empower and Millennium32 connections
Empower and Millennium32 software perform data acquisition, processing,
and management of chromatographic information. This software requires the
detector's analog signal to be converted to a digital form.
I/O signal connections
Empower and Millennium32 are menu-driven applications specifically
designed by Waters for chromatographers. Use the software to:
Generate and print reports
Store information (or data) in a central area and share this information
with users who have proper security access
To connect the 432 Detector to an Empower or Millennium32 computer, be sure
Connect the Bus Satellite Interface (SAT/IN) module to the Bus
Laboratory Acquisition and Control/Environment (LAC/E™) card in the Empower computer, Millennium32 computer, acquisition client, or LAC/E32.
Connect the 432 Detector to the Bus SAT/IN module (Channel 1 or 2).
Remove the IEEE-488 cable from the rear panel of the 432 Detector, if it
is connected.
The 432 Detector is in local mode when it is connected to an Empower and Millennium32 computer.
Bus SAT/IN module
The Waters Bus SAT/IN module translates analog signals into digital form. It
then transmits these digital signals to the Bus LAC/E card inside the workstation, acquisition client, or LAC/E32.
Installing the Detector
Bus SAT/IN module (front panel)
Waters SAT/IN Module
CHANNEL 1 CHANNEL 2
Tip: To prevent damage to the unit, always disconnect the power cord at either
the wall outlet or the power supply before you attach or remove the power
connection to the Bus SAT/IN module. The Bus SAT/IN module does not have
a power switch.
Connecting the Bus SAT/IN module to the Bus LAC/E card
The Bus SAT/IN module connects to the Bus LAC/E through an I/O
distribution box.
To connect the Bus SAT/IN module to the Bus LAC/E card:
1. Use the I/O distribution cable to connect the I/O distribution box to the
9-pin I/O distribution port on the Bus LAC/E card at the back of the Millennium32 computer.
2. Use a serial cable to connect the data terminal on the back of the Bus
SAT/IN to a port of the I/O distribution box.
3. Configure the serial port for the Bus SAT/IN module as described in the
Empower or Millennium32 installation and configuration guides.
I/O signal connections
Bus SAT/IN to Bus LAC/E connections
I/O Distribution Por t (9-pin)
of Bus LAC/E Card
I/O Distribution
I/O Distribution Box
I/O Distribution Box
AC to DC Converter
Installing the Detector
Connecting the Bus SAT/IN module to the 432 Detector
The Bus SAT/IN module connects to the 432 Detector as shown below. Refer to
the procedure following the figure and the
complete details.
Caution: To prevent damage to the unit, do not plug in the power cord of
the Bus SAT/IN module until you perform all of the procedures
described in the Waters Bus SAT/IN Module Installation Guide.
Bus SAT/IN to 432 Detector connections
Waters 432 Detector
Waters SAT/IN Module
CHANNEL 1 CHANNEL 2
To connect the 432 Detector to the Bus SAT/IN module:
1. Connect the white wire of the analog cable (included with the Bus
SAT/IN module) to the Int + terminal on the rear panel of the 432
Detector. Connect the black wire to the Int – terminal.
I/O signal connections
2. Connect the other end of the cable to either the Channel 1 or Channel 2
connector on the front panel of the Bus SAT/IN module.
3. Connect the Event In terminals of the channel you chose in the previous
step to the Inject Start output signal of the Waters Alliance® solvent
delivery system or the Waters 717plus (or equivalent) Autosampler.
4. Remove the IEEE-488 cable from the rear panel of the 432 Detector, if it
is connected.
The connections from the 432 Detector to the Bus SAT/IN are summarized
Bus SAT/IN cable connections
432 Detector I/O
Bus SAT/IN cable
Bus SAT/IN connector
connector terminal
Int (+)
Data module connections
This section describes how to connect the analog output signal from the 432
Detector to the Waters 746 Data Module.
Caution: Remember to meet the regulatory requirements of immunity
from external electrical disturbances that may affect the performance of
this instrument, do not use cables longer than 9.8 feet (3 meters) when
connecting to the screw-type barrier terminal strips. In addition, ensure
you always connect the shield of the cable to chassis ground.
Installing the Detector
To send the analog output signal from the 432 Detector to a Waters data
module, connect the signal cable in the 432 Detector Startup Kit as described
Data module signal cable connections
432 Detector I/O
746 terminal
Marker out signal
The Marker Out terminals of the 432 Detector provide a contact closure
output signal when either of the following events occurs:
Chart Mark key is pressed
Marker In terminals are shorted together
Use the signal to start a Waters 746 Data Module by connecting a signal cable
to the module's data cable.
Data module chart mark cable connection
432 Detector I/O
746 cable
Join to both Remote
Start wires (white and
Chart recorder connections
To connect the 432 Detector to a chart recorder:
1. Attach the Recorder cable (see he 432 Detector REC
output terminals, as indicated in th
I/O signal connections
2. Connect the cable shield to the ground lug on the 432 Detector rear
3. Connect the other end of the cable to the 10-mV input terminals on the
chart recorder.
Chart recorder cable connections
432 Detector I/O
Chart recorder
Chart marker input connections
The 432 Detector accepts a chart mark (start inject) signal from the following
Waters 717plus Autosampler
Any other device that provides a compatible switch closure
Waters 717plus Autosampler
To connect the 432 Detector to a Waters 717/717plus Autosampler, connect a
signal cable as indicated in the table below.
Autosampler chart mark cable connections
432 Detector I/O
connector terminal
Marker In (+)
Either Inject Start terminal of a pair
Other Inject Start terminal of the same pair
Installing the Detector
Auto Zero input connections
The voltage at the Recorder and Integrator outputs is set to the user-selected
balance offset level when a contact closure occurs between the Auto Zero
terminals. This section describes how to connect the 432 Detector to the
following devices (so that an auto zero occurs at the injection point):
Waters 717plus Autosampler
Any other device that provides a compatible switch closure
Waters 717plus Autosampler
To connect the 432 Detector to a Waters 717plus Autosampler, connect a
signal cable as indicated in the table below.
Autosampler Auto Zero cable connections
432 Detector I/O
connector terminal
Auto Zero (+)
Either Inject Start terminal of a pair
Other Inject Start terminal of the same pair
Alliance Separations Module connections
Connect the detector to Waters Alliance Separations Modules, when it is not under the control of the Millennium32 software, to perform the following tasks:
Auto-Zero on inject
Chart mark on inject
Generating Auto-Zero on inject
To generate the Auto-Zero function on the 432 Detector at the start of an
injection, make the connections summarized in the
I/O signal connections
Connections for generating Auto-Zero on inject
Alliance Separations Modules (B
432 Detector (A inputs)
inputs and outputs)
Pin 1 Inject Start
Pin 2 Inject Start
Before you can generate an Auto-Zero from an Alliance Separations Module,
you must configure the Auto-Zero signal at the 432 Detector front panel. The
default Auto-Zero signal is Low.
Alliance Separations Module connections to the 432 Detector
Auto-Zero on inject
Waters 432 Detector
B (inputs and outputs)
4 Lamp On/Off +5 Lamp On/Off -
Hold inject 1 –
8 Ground – Marker in
Hold inject 2 –
Chart out +Chart out –
Generating chart mark on inject
To generate the chart mark function at the start of an injection, make the
connections summarized in the table below and illustrated in the
Installing the Detector
Connections for generating chart mark on inject
Alliance Separations Modules (B
432 Detector (A Inputs)
inputs and outputs)
Pin 1 Inject Start
Pin 2 Inject Start
Before you can generate a chart mark from an Alliance Separations Module,
you must configure the chart mark signal at the front panel. The default chart
mark signal is Low.
Alliance Separations Module connections to the 432 Detector
chart mark on inject
Waters 432 Detector
B (inputs and outputs)
4 Lamp On/Off +5 Lamp On/Of
Hold inject 1 –
Hold inject 2 –
Making fluidic connections
Fluid lines to a column and waste container connect to the front of the 432
these connections:
Making fluidic connections
Cut the tubing.
Assemble compression fittings and ferrules.
Connect the tubing to the detector.
This section will guide you through each of these procedures.
Caution: Conductivity detection is sensitive to flow rate fluctuations. If
you use a non-Waters pump or a Waters pump without the SILK
microflow compensation algorithm, you must install the pulse dampener
kit supplied in the Startup Kit for optimum performance. Refer to the
installation procedure in this section.
Conductivity Detector
a ste (18 inches.
(18 inches, 0.000-inch ID)
Cutting stainless steel tubing
You need the following tools to cut stainless steel tubing:
A file with cutting edge
Two cloth- or plastic-covered pliers
Installing the Detector
To cut the tubing:
1. Measure the length of 1/16-inch OD, 0.009-inch ID, stainless steel
tubing you need to make the following connections:•
Column to the detector inlet
Detector outlet to a suitable waste container
2. Use a file with a cutting edge to scribe the circumference of the tubing at
the desired length.
3. Grasp the tubing on both sides of the scribe mark with cloth-covered
pliers. Gently work the tubing back and forth until it separates.
4. File the ends smooth.
Cutting polymeric tubing
Waters chromatography systems are supplied with a tubing cutter (similar to
the one in the ) to facilitate
cutting polymeric tubing. This section presents the recommended procedure
for using the tubing cutter.
Tip: To avoid bandspreading caused by angled cuts, always use a tubing
cutter. Angled cuts leave unswept dead volumes at the connection junction
due to the poor fit of the tubing against the connector or port.
To cut a length of polymeric tubing:
1. Estimate the length of tubing required to connect the components. Allow
slack so that the tubing is not pulled tightly around sharp corners.
2. Insert the tubing into the cutter so that the tubing extending from the
metal side is the length required. Use the proper hole to have a snug
enough fit so that the tubing is not flexed by the blade when you cut it.
Making fluidic connections
Cutting polymeric tubing
3. Press down on the razor blade to cut the tubing. Discard the excess
tubing that extends from the clear side of the cutter.
4. Inspect the cut for burrs or scratches and for the perpendicularity of the
Assembling compression fittings
To assemble each compression fitting:
1. Slide the compression screw over the tubing end, followed by the ferrule.
2. Mount the ferrule with its taper end facing the end of the tubing.
Ferrule and compression screw assembly
Compression screw
0.0009-inch ID tubing
0.009-inch I.D. Tubing
Installing the Detector
Connecting to the 432 Detector
To make connections at the column outlet and detector inlet, and at the
detector outlet:
1. Install a compression screw and then a ferrule on the length of
0.009-inch tubing from the column outlet. Use stainless steel fittings on
stainless steel tubing and PEEK fittings on PEEK tubing.
Tip: If you are using a column with 1/4–28 end fittings and there is a
length of tubing with 1/4–28 fittings on each end, use the 1/4–28 to
Z-detail adapter (included in the Startup Kit) to connect this tubing to
the tubing that leads to the detector inlet.
The Waters IC-Pak C column comes supplied with a length of tubing
that has a 1/4–28 fitting on one end (column outlet) and a Waters
compression screw and ferrule on the other end (detector inlet).
2. Push the free end of the tubing as far as it will go into the IN fitting on
the 432 Detector. While you hold it there, use a 5/16-inch open-end
wrench to tighten the compression screw 3/4-turn past finger-tight.
Tip: The 432 Detector and IC-Pak series of columns have very deep
3. Remove the compression screw and tubing from the connection and
verify that fluid can flow freely.
4. Reconnect the tubing to the IN fitting, making sure to push the tubing
all the way into the fitting.
5. Install a ferrule on an 18-inch length of 0.009-inch tubing and connect it
to the OUT connection on the 432 Detector. Use stainless steel fittings
on stainless steel tubing and PEEK fittings on PEEK tubing.
6. Place the other end of the tube in a waste container. If you are using any
Teflon tubing, attach it after the stainless steel or PEEK tubing.
Installing the pulse dampener
To achieve the best performance from the 432 Detector in a chromatographic
system with a non-Waters pump, Breeze™ software, or Waters HPLC 515
Pump, you must install the pulse dampener kit supplied in the Startup Kit.
The pulse dampener is not required if you are using a Waters 2695
Separations Module.
Making fluidic connections
To install the pulse dampener between the pump and the injector:
1. Assemble the pulse dampener (see the
) using the instructions in the pulse dampener kit.
2. Connect the large-ID (0.020-inch) tubing to the pump outlet using a
stainless steel compression screw and ferrule.
3. Connect the small-ID (0.009-inch) tubing to the injector inlet using a
stainless steel compression screw and ferrule.
4. Disconnect the tubing from the injector inlet.
5. Pump ASTM Type I reagent water at £ 2 mL/min through the pulse
dampener assembly until you see a constant stream exiting from the
restrictor assembly outlet line.
6. Reconnect the tubing to the injector inlet.
0.009 inch I.D.
Installing the Detector
Passivating the system
Passivating the system removes potential contamination from the wetted
surfaces of all system components. Perform passivation on a new system, and
subsequently, whenever you suspect that contamination may have occurred.
elp diagnosing performance problems.
Use this procedure for Waters hardware only. For other equipment, check
with the manufacturer before you continue with this procedure.
Caution: If you are installing the 432 Detector into an existing Waters
system, replace the pump seals before you passivate. Use the new pump
seals supplied in the Startup Kit and refer to the replacement procedure
in the pump manual.
To passivate the system:
1. Replace the column with a union fitting.
2. If the system is not new, flush it thoroughly with ASTM Type I reagent
water to remove any residual solvents or salts.
3. Connect the power cord to the 432 Detector and plug the other end into
an AC power outlet. Push the 432 Detector power switch to turn on the
Warning: To avoid chemical hazards, always wear safety glasses and
gloves when you are using solvents.
4. Prime the pump with 6 N nitric acid (HNO3) and run it at a flow rate of
1.2 mL/min for 20 minutes to passivate all the wetted parts of the
detector. Press the Clear key to stop the overrange alarm.
5. Stop the pump.
6. Remove the inlet line from the nitric acid and place it in ASTM Type I
reagent water.
7. Flush the system using one of the following methods:
Prime and start the pump, then flush it with ASTM Type I reagent
water at 1.2 mL/min until you observe a consistent reading of less
than 20 μS (base range set to 50 μS).
Passivating the system
Flush the system overnight with 100% methanol at a reduced flow
rate. By the next morning the system will be passivated and ready
Tip: If you are using a pump with seal-wash capability, skip step 8.
8. Use a syringe to flush the back of the pump seals and pistons by slowly
running about 5 mL of water into the top hole in the baseplate of the
pump heads. Place a tissue under the baseplates to absorb the water.
9. Set the pump flow rate to 0.0 mL/min. It is not necessary to turn off the
432 Detector unless it will be idle for an extended period (14 days).
For best results, always leave the power on to maintain cell temperature; it
takes a minimum of 2 to 3 hours once the detector is turned on to equilibrate
the flow cell at the selected operating temperature.
Verifying the detector
This procedure is a guideline for verifying that the detector works correctly
within its expected operational range. The detector is calibrated before
shipping, and recalibration is not normally required.
Verify the detector when any of these conditions apply:
When you replace the flow cell
To verify accuracy
When you make adjustments
Tip: You need solution of 1 mM potassium chloride (KCl) to calibrate the
Tip: Waters suggests one of its Technical Service Representatives perform this
To perform the calibration procedure:
1. Turn on the 432 Detector and set the temperature control to 35 °C.
Allow 2 to 3 hours for the temperature in the flow cell to equilibrate.
2. Set the base range to 200 μS.
3. Set the Filter Time Response to Fast.
Installing the Detector
4. Pump 1 mM KCl solution through the detector (without a column in
5. Verify that the front panel output is 147 μS ± 5 μS.
Verifying the detector
Installing the Detector
3 Operating the Detector
This chapter contains:•
A description of front panel controls and displays
Procedures for starting up, shutting down, and long-term storage
Recommended operating practices
Controls and indicators
The figure below illustrates the controls and indicators on the front panel of
the 432 Detector.
Front panel
Waters 432Conductivity Detector
Power switch
The power switch (located in the lower-right corner of the front panel) controls
power to the 432 Detector. Upon startup, an initialization routine verifies the
data in ROM memory, tests RAM memory function, and checks for any
internal leakage or an eluent conductivity over-range condition.
The display shows instrument status and parameter values in two
20-character lines of text. Upon startup, Waters 432 Self Check appears
Operating the Detector
briefly. If any error conditions are detected during startup or normal
operation, the appropriate error message is displayed.
The main screen shows the measured conductivity, as well as the base range
and sensitivity settings. When you set an operating parameter, the display
shows the selected or entered value.
A corresponding error message is displayed if one of the following conditions
ROM/RAM error (checked during startup only)Error: ROM/RAM
Leakage detectedError: Leak
Temperature control failureError: Temp
Over-range (above base range setting)Error: Over Range
Overflow (above 10,000 μS)Error: Over Flow
Press the Clear key to clear an error alarm and message. For a continuing
error condition, the error message remains after the audio alarm is cleared.
Use the keypad to control the operat
describes the function of each key.
Controls and indicators
Tip: Three keys (Balance, Sensitivity Range, and the numeral 1) perform an
alternate function when they are preceded by the Shift key.
Function
Remote key: Toggles between local and remote
operating modes. In remote mode, the light above the
key is on and all other front panel controls are
Polarity key: Toggles the polarity of the signal to the
external chart recorder and integrator. When positive
polarity is selected, the light above the key is
Base Range key: Sets the base sensitivity range of
the 432 Detector to the appropriate value for the
eluent being used. The base sensitivity is set to one of
ten steps, from 10 μS (maximum gain) to 10,000 μS,
using the Up and Down keys or the numeric keypad.
Sensitivity Range key: Sets the sensitivity range
multiplier of the 432 Detector. The sensitivity range
has twelve steps, from 0.0001 (maximum sensitivity)
to 1.0 (available only with 100 μS multiplier setting),
and is set using the Up and Down keys or the numeric
keypad. The 10-mV full-scale recorder response is
calculated by multiplying the Base Range by the
Sensitivity Range to obtain a value of "x" μS / 10 mV
FS. The recorder range is 1 to 0.0001 for the 100 μS
setting and 0.1 to 0.0001 for the two lower settings.
Shift key then Sensitivity Range key: Sets the
sensitivity range multiplier of the integrator to 100,
50, or 10 μS using the Up and Down keys or the
numeric keypad; the integrator output is 100, 50, or
10 μS/1 V, respectively.
Operating the Detector
Key descriptions (Continued)
Function
Balance key: Manually sets the offset (%) of the
signal to the external chart recorder. (Use the
numeric keypad or Up and Down keys.)
Shift key then Balance key: Manually sets the
offset (%) of the signal to the integrator. (Use the
numeric keypad or Up and Down keys.)
Shift key after Balance key: Changes the polarity
of the offset. Allowable values are –100 to +100%.
Temperature key: Sets the temperature of the
detection cell. Use the Up and Down keys or the
numeric keypad to turn temperature control off
(Setting 0) or select one of the following eight
settings: 30, 35, 40, 45, 50, 55, 60, or 65 °C. The light
above the key is illuminated when the temperature
control is on.
Response key: Sets the response time constant of
the 432 Detector to optimize signal-to-noise ratio. Use
the Up and Down keys or the numeric keypad to
choose Setting 1 (Fast, 0.25 sec) for very narrow
peaks, Setting 2 (Standard, 0.5 sec), or Setting 3
(Slow, 1.0 sec) to detect wider peaks. Setting 2 is used
for most applications.
Auto Zero key: Automatically zeros the Recorder
and Integrator signals to the specified Recorder
Balance and Integrator Balance offsets, respectively.
Auto Base key: Automatically sets the base range of
the 432 Detector to the appropriate value for the
eluent being used. This is the next highest setting
above the actual background conductivity of the
Controls and indicators
Key descriptions (Continued)
Function
Shift key: Press the Shift key before, not along with,
other keys to access additional functions and also to
change polarity when you set balance offset values.
When the Shift key is pressed, an asterisk (*) appears
at the right side of the display; press Shift again to
return to normal mode.
Shift key then Balance key: Displays the
integrator balance offset value. When setting the
balance offset, press Shift to change polarity.
Shift key then Sensitivity Range key: Displays
integrator range value.
Shift key then 1 key: Displays the current, actual
value of the chart recorder balance offset. Press
Enter to return to the main screen.
Chart Mark key: When this key is pressed, a
1-second, 1-mV signal is sent to the Recorder
terminals and a 1-second contact closure is sent to the
Marker Out terminals.
Enter key: When you manually set offsets,
sensitivity range, or base range, pressing Enter
records the displayed value and returns the display to
the main screen. The Enter key is also used to access
the beep setting function.
Clear key: Erases a value input from the keypad.
The Clear key is also used to clear an error alarm and
message. For a continuing error condition, the error
message remains after the audio alarm is cleared.
Up key: Increments the current parameter setting.
Operating the Detector
Key descriptions (Continued)
Function
Down key: Decrements the current parameter
You can set the 432 Detector to beep when a key is pressed and/or an error
condition is detected.
Use the Clear key to stop an error alarm. For a continuing error condition,
the error message remains after the beep is cleared.
To set the beep function, follow the procedure in the table below.
Setting the beep function
Accesses the beep function parameters.
. (decimal point)
Turns on the beep-on-error function.
Turns off the beep-on-error function.
Turns on the beep-on-keystroke function.
Turns off the beep-on-keystroke function.
Saves settings and returns to the main
Tip: Since the void volume in many separations contains highly conductive
counter-ions, the error alarm sounds upon each injection.
to silence the beep-on-error alarm.
Controls and indicators
Startup and shutdown
Perform the following procedure to start the 432 Detector. Typically, this
procedure is done at the beginning of each workday.
Tip: This procedure assumes that the flow cell has stabilized at the selected
temperature (minimum 2 to 3 hours). Standard practice is to leave the
detector powered and with the temperature control on unless the instrument
will be unused for several days.
Set the temperature at least 5 °C above the highest ambient temperature
expected for the duration of the application.
1. Prime the pump with properly degassed eluent and set the flow rate to
1.2 mL/min or to the flow rate recommended for your particular column
or application. Do not sparge eluents, since sparge gasses may contain
ionic contaminants.
2. Set the response (time constant) to the desired setting by pressing the
Response key. A standard setting (0.5 seconds) is preferred for most
3. Set the base value by pressing the Auto Base key or by manually
entering the base range that is the next highest setting above the
eluent's background conductivity.
4. Turn on the recorder/integrator and run the system until the baseline
5. Depending on whether you are using a recorder or an integrator, do one
of the following actions:•
If you are using a 10-mV recorder connected to the Recorder
terminals on the rear panel, select the desired sensitivity by
pressing the Sensitivity Range key, then the appropriate Up or
Down arrow key.
If you are using an integrator connected to the Integrator terminals
on the rear panel, select the desired sensitivity by pressing the Shift
and Sensitivity Range keys, then the appropriate Up or Down arrow
Operating the Detector
6. Zero the recorder/integrator by pressing the Auto Zero key or have the
Auto Zero terminals of the rear panel I/O terminal strip connected to
your manual injector or autosampler.
The 432 Detector is now ready for operation.
To eliminate the need to allow time for the flow cell temperature to
equilibrate, leave the 432 Detector turned on at the end of the workday or
workweek. Set the temperature control to the operating temperature and the
pump flow rate to 0.01 to 0.1 mL/min (depending on the pump).
If the 432 Detector is to be removed from a system for storage or if the system
itself is to be stored for a long time, flush the detector/system with 100%
water, then 100% HPLC-grade methanol. Leave the methanol in the system
after shutdown. If you are removing the 432 Detector from the system, seal
the inlet and outlet bulkheads with dead-end fittings or a loop of tubing.
Observe the following recommendations for best detector performance.
The 432 Detector should be powered up and set at the desired operating
temperature for two to three hours before use. Select a temperature at least
5 °C above the highest ambient temperature expected during the duration
of the application. The detector is usually set at 35 °C, but it should be set
higher if the ambient temperature will exceed 30 °C.
You may choose to leave the 432 Detector powered up overnight at a flow rate
of 0.01– 0.1 mL/min (depending on the pump) to minimize the daily
reequilibration time.
A drifting baseline is one indication that the temperature of the flow cell is not
uniform across the flow cell or stable over time.
Base range
The Base Range is normally set at the next setting above the background
conductivity of the eluent. For example, if the conductivity of borate/gluconate
eluent is 270 μS, set the Base Range to 500 μS.
The Integrator output is not attenuated; signals should be below 1 V. Set the
Integrator output to 10 μS/V for small signals or to 50 μS/V when you expect a
signal greater than 10 μS. If you are using the 432 Detector with chemical
suppression, set the integrator output to 100 μS/V.
The Recorder output is attenuated and the Sensitivity Range should be
adjusted to provide the appropriate output level.
Signal polarity depends on eluent conductivity. If necessary, press the
Polarity key to obtain peaks rather than dips.
Replace your eluent reservoir filter regularly. When you analyze cations, use
an all-plastic eluent reservoir filter. Filter and degas eluents to prolong
column life, reduce pressure fluctuations, and decrease baseline noise. When
you change eluents, flush the flow cell and associated tubing thoroughly with
the new eluent.
Operating the Detector
4 Performing Ion Analysis
This chapter provides essential information about ion analysis
techniques. Two representative columns serve as typical examples: the
Waters IC-Pak A for anions and the IC Pak C M/D for cations. The
following topics are discussed:•
Configuring the system
Selecting and preparing eluents
Preparing and injecting standards
Also refer to the manufacturer's manual for the particular column you
are using. A recommended source for more information about ion
analysis in general is Ion Chromatography: Principles and Applications
by Paul R. Haddad and Peter E. Jackson, Elsevier Science Publishing,
New York, 1990.
Contents
To obtain full performance from the 432 Detector in chromatographic
applications, observe the guidelines presented in this section regarding:
Sample preparation
Water purity (the absence of conductivity) is the most important consideration
in ion analysis.
Tip: Using water other than ASTM Type I reagent water will compromise the
accuracy of your results.
Freshly drawn ASTM Type I reagent water, conforming to ASTM specification
D1193, with total organic carbon <100 ppb is recommended. Sophisticated
laboratory water systems that use a combination of reverse osmosis, mixed
bed ion exchange, and carbon adsorption cartridges produce ASTM Type I
reagent water, and are recommended for ion chromatography applications. Do
not use HPLC-grade water or distilled water.
Caution: To avoid damage to the detector flow cell, do not allow the flow
cell to dry out.
Use plastic to contain all anion and cation samples, cation standards, and
cation eluents. When you analyze trace level ions in water, polystyrene
containers such as tissue culture flasks are recommended; polypropylene or
polymethylpentene containers suit most other applications. Use polystyrene
tissue culture flasks for long-term storage.
If your system operates on Breeze software or contains a 2695 Separations
Module, use 4-mL polycarbonate vials to hold your samples and standards.
Caution: Avoid glass containers (which tend to leach sodium cations)
when you are analyzing for cations.
Performing Ion Analysis
Preparing containers for low-level analysis
To prepare plastic containers for low-level analysis:
1. Soak all containers for 5 hours with a 1:1 solution of nitric acid (HNO3)
and ASTM Type I reagent water.
2. Rinse with plenty of ASTM Type I reagent water. The containers are
ready for analysis in the ppm range.
3. For analysis in the ppb range, fill each container completely with ASTM
Type I reagent water and let soak overnight.
Certain applications that involve ppb level analysis may require container
considerations beyond the scope of this manual. For further instructions on
trace metal cleaning of plasticware, see "Selection and Cleaning of Plastic
Containers for Storage of Trace Element Samples," JR Moody and RM
Lindstrom, Analytical Chemistry, v. 49, Dec 1977, pp. 2264-67, or contact the
Waters Technical Services Department.
To avoid contamination, always rinse a syringe two to three times with ASTM
Type I reagent water before you draw standards or samples for injection.
High-pH eluents (such as hydroxide eluent) absorb atmospheric CO2, which
slowly acidifies the eluent causing baseline drift and retention time changes.
To minimize carbonate absorption, connect a soda lime (Ascarite®) tube to
the eluent bottle as follows:
1. Insert a 3/4-inch (2-cm) piece of glass wool in one end of a polyethylene
tube with end fittings. Attach the end fitting.
Warning: To avoid chemical burns, wear gloves, lab coat, and eye
glasses when you are handling soda lime.
2. Fill the tube with soda lime (Ascarite) until it reaches 3/4 inches (2 cm)
from the top.
3. Add another piece of glass wool to the other end of the tube and attach
the end fitting.
4. Drill a hole in the cap of the reagent bottle. The hole should be large
enough to accommodate the end fitting. Drill a second hole for the pump
5. Pass the pump inlet line through the hole. Seal the hole with paraffin
6. Change the soda lime in the tube when it is exhausted.
Soda lime tube
Polypropylene ube
Performing Ion Analysis
Sample preparation is very important in ion analysis. Contact the Waters
Technical Services Department, if you need assistance.
As a general rule, to analyze a sample of completely unknown ionic
concentration, initially prepare at least a 1:100 dilution and inject 100 μL. For
best results, injections should contain a total anion concentration of no more
than 300 ppm for the IC-Pak A column or a total cation concentration of no
more than 10 ppm per ion for the IC-Pak C M/D column.
The sample volume (usually 100 μL) generally equilibrates to the pH of the
eluent upon injection. However, for samples with pH values that differ greatly
from that of the eluent (for example, strong acids and bases), bring the sample
pH close to that of the eluent before you inject the sample, if possible.
Do not inject concentrated samples directly into the mobile phase. Direct
injection may cause precipitation of the salts in the sample. Dissolve (or
dilute) samples in an appropriate volume of the mobile phase first. If you must
use other solvents, watch for precipitation upon injection into the eluent.
Always filter samples before you use them.
Cationic samples that contain organic amines may exhibit hydrophobic
interaction between the mobile phase and packing. You may use a
water-miscible organic mobile phase, such as acetonitrile, as a modifier to reduce this. Pretreat the sample with a Sep-Pak® C18 cartridge to remove
Configuring the system
system configuration. Refer to
the procedures to cut tubing and assemble fittings.
Configuring the system
System configuration for ion analysis
Waaters In-Line Degasser
ters in-line degasser*
† Required for Waters pumps without SILK or non-W
tRequired for non-Waters pumps or Waters pumps with Breeze software, such as the HPLC 515
If your system uses a non-Waters pump or a Waters pump with Breeze
software, such as the HPLC 515, use a pulse dampener (supplied in the
Startup Kit) to achieve the best performance from the 432 Detector.
Install the pulse dampener between the pump and the injector, as described in
Eluents for ion analysis
This section describes how to select, prepare, and use eluents for ion analysis.
Caution: Never recirculate eluents. Ions from sample and standard
injections progressively contaminate a recirculating eluent.
Observe the following guidelines when you prepare eluents for ion analysis:
Use only ASTM Type I reagent water with total organic carbon
<100 ppb.
Use the highest purity salts and reagents available.
Performing Ion Analysis
A pH meter is recommended for checking the pH of eluents; care should
be taken to avoid cross contamination. Adjust the pH with potassium
hydroxide (KOH) or lithium hydroxide (LiOH). For eluents such as
octane sulfonate, test an aliquot of the eluent with pH paper. Never
immerse pH paper directly into a batch of eluent.
Use the following formula to prepare eluents:
Formula Wt of Salt x Molarity = g/L Salt
Eluent filtering and degassing
The Waters Solvent Clarification Kit is recommended for eluent filtration and preliminary degassing. Durapore® 0.22-mm filters can be used for all ion
chromatography eluents. Millipore 0.45-mm HATF filters may be used for
aqueous eluents containing no organic modifier. For eluents containing
organic modifier, use the Durapore filters.
Caution: To avoid contamination when you analyze for cations,
minimize the time that the eluent is in contact with the glass filtration
apparatus and transfer the eluent to a suitable pre-cleaned plastic
container as soon as possible.
After you install a new filter, pass 20 to 30 mL of eluent through the filter
under vacuum. Turn off the vacuum, swirl the eluent throughout the flask and
discard. Reattach the flask to the filter apparatus and filter the remaining
eluent. As soon as filtration is complete, transfer the eluent to a precleaned
plastic container, introducing the least possible amount of bubbles in the
process.
The Waters In-line Degasser is recommended for continuous online degassing.
Preparing anion eluent
This section presents the procedure for the preparation of sodium
borate/gluconate concentrate and eluent.
Consult the manufacturer's manual for your column (IC-Pak Column and
Guard Column Care and Use Manual included with Waters columns) for
additional instructions on the selection and preparation of eluents.
A recommended source for more information about ion analysis in general is
"Ion Chromatography: Principles and Applications," by Paul R. Haddad and
Peter E. Jackson, Elsevier Science Publishing, New York, 1990.
Eluents for ion analysis
Preparing lithium borate/gluconate concentrate
To prepare sodium borate/gluconate concentrate, re
Preparing cation eluent
To prepare 1 L of cation eluent, refer to.
Standards for ion analysis
This section describes how to prepare and inject ion standards.
Tip: It is recommended to purchase certified 1000-ppm anion standards
instead of preparing them manually. Certify all manual standards against
National Institute of Science and Technology traceable standards.
Standard concentrations in this manual are defined in terms of mass. For
example, 1 mg of sample per liter of water equals a 1 ppm concentration, since
1 L of water has a nominal mass of 1 kg (0.997 kg at 25 °C).
1 part per thousand = 1 mg/mL = 1 g/L = 1000 ppm1 part per million (ppm) = 1 μg/mL = 1 mg/L = 1000 ppb1 part per billion (ppb) = 1 ng/mL = 1 μg/L = 1000 ppt1 part per trillion (ppt) = 1 pg/mL = 1 ng/L
For accurate quantitative results, do not store standards beyond the
approximate periods listed in the table below. Be aware that shelf-life depends
on many factors and may be significantly shorter than shown here.
Shelf-life of standards
Nitrite and carbonate concentrates
Performing Ion Analysis
Shelf-life of standards (Continued)
All other anion concentrates
Cation concentrates
Cation standards must be stored in properly prepared plasticware. See
Preparing anion standards
This section presents the procedure for preparing a 7-anion standard. If a
simpler standard suffices, follow the procedure, but select only three or four
salts, such as sodium chloride, sodium nitrate, and sodium sulfate.
Always use salts of at least reagent-grade purity. If you require quantitative
results or you use hygroscopic salts, dry the salts overnight at 80 °C before you
make solutions. Store the dried salts in a desiccator.
Preparing a 7-anion standard
To prepare a 7-anion standard:
1. Weigh out the amounts of dry salts shown in the table below or use the
following formula to calculate the amount for a salt not listed:(Mol. Wt. Salt / Mol. Wt. Cation) x 0.1 = g Salt
Salts for anion standard concentrates
Salt (anion)
Weight (mg)
Sodium fluoride (F–)
Sodium chloride (Cl–)
Sodium nitrite (NO –)
Potassium bromide (Br–)
Sodium nitrate (NO –)
Potassium phosphate,
monobasic (HPO 2–)
Sodium sulfate (SO 2–)
Standards for ion analysis
2. Place each salt in a separate plastic100-mL volumetric flask and dilute
to the mark with ASTM Type I reagent water. Each concentrate
contains 1000 ppm of the anion.
3. Combine the amounts listed in the table below in a 100-mL volumetric
flask with ASTM Type I reagent water.
Anion concentrate dilutions
Final Concentration
Injecting anion standards
To inject a standard, obtain the following materials:
1-cc disposable plastic syringe – Pharmaseal® Stylex® disposable
syringe with a Luer Slip® tip, or equivalent.
Autoinjector or manual injector with 100-μL loop – Ion
chromatography commonly uses a 100-μL injection volume. When you
use a fixed loop, overfill a minimum of three times.
Performing Ion Analysis
Injecting the standard
To inject the standard:
1. Set up the 432 Detector as follows:
Base Sensitivity = 500 μS
Integrator Sensitivity = 10 μS/V
Recorder Sensitivity = 0.01 (strip chart)
Response = STD (0.5 seconds)
Temperature = 35 °C
2. Equilibrate the 432 Detector as described in
3. Rinse a 1-cc disposable plastic syringe two or three times with ASTM
Type I reagent water, then load the standard.
4. Place the syringe tip into the sample loading port and overfill the 100 μL
loop at least three times (that is, 300 μL).
5. Inject the sample.
representative chromatogram of the 7-anion standard run on an IC-Pak A (4.6
mm x 5.0 cm) column with borate/gluconate eluent at 1.2 mL/min flow rate.
The separation of the standard typically takes 12 to 15 minutes with this
Standards for ion analysis
Chromatogram of a 7-anion standard
Preparing cation standards
This section presents the procedure for preparing an 8-cation standard. If a
simpler standard suffices, follow this procedure selecting only those salts that
you want in the standard. For accurate quantitative results, use only properly
prepared plasticware and do not store standards beyond the recommended
shelf-lives listed in the .
Preparing cation standard concentrates
Tip: It is recommended that you use certified 1000-ppm cation standards not
prepared in acid with this method.
Performing Ion Analysis
To prepare concentrated stock solutions for an 8-cation standard (prepare
fewer types of cations, if a simpler standard suffices):
1. Weigh out the amounts of dry sa
to calculate the amount for a salt not listed.
(Mol. Wt. Salt / Mol. Wt. Cation) = g SaltIf you choose to use other salts, be sure to avoid any combinations that
will form a precipitate.
Salts for cation standard concentrates
Weight (g)
Lithium hydroxide monohydrate (Li+)
Sodium chloride (Na+)
Ammonium chloride (NH +
Potassium chloride (K+)
Magnesium nitrate hexahydrate (Mg2+)
Calcium nitrate tetrahydrate (Ca2+)
Strontium nitrate tetrahydrate (Sr2+)
Barium chloride dihydrate (Ba2+)
2. Place each salt in a separate plastic1-L volumetric flask and dilute to
the mark with reagent-grade water. Each concentrate contains
1000 ppm of the cation.
Standards for ion analysis
Preparing an 8-cation standard
To prepare 1 liter of 8-cation standard:
1. Add the volume of stock (concentrate) standard listed in the table below
to a plastic 1-L volumetric flask.
Cation concentrate dilutions
Amount (mL)
Final concentration (ppm)
2. Fill the flask to the mark with ASTM Type I reagent water.
Injecting cation standards
To inject the standard, obtain the following materials:
0.1 mM EDTA/ 3 mM HNO cation eluent – Refer to
1-cc disposable plastic syringe – Pharmaseal® Stylex® disposable
syringe with a Luer Slip® tip, or equivalent.
Injector or autosampler with a 100-μL loop – Ion chromatography
commonly uses a 100-μL injection volume. When you use a fixed loop,
overfill a minimum of three times.
Performing Ion Analysis
Injecting the standard
Tip: You can substitute the method desc
, for the following procedure.
To inject the standard.
1. Set up the 432 Detector as follows:
Base Sensitivity = 2000 μS
Integrator Sensitivity = 50 μS/V
Recorder Sensitivity = 0.01 (strip chart)
Response = STD (0.5 seconds)
Temperature = 35 °C
Polarity = – (negative)
2. Equilibrate the 432 Detector as described in
3. Rinse a 1-cc disposable plastic syringe two or three times with ASTM
Type I reagent water, then load the standard.
4. Place the syringe tip into the sample loading port and overfill the 100-μL
loop at least three times (that is, 300 μL).
5. Inject the sample.
representative chromatogram of an 8-cation standard run on an
IC-Pak C M/D column with 0.1 mM EDTA/3 mM HNO eluent at 1.0 mL/min
flow rate. The separation of the standard typically takes 20 to 25 minutes with
Standards for ion analysis
Chromatogram of an 8-cation standard
Performing Ion Analysis
This chapter contains information about maintaining the 432 Detector
and troubleshooting charts to help you isolate and correct problems.
Warning: To avoid the possibility of electric shock, power off the
detector and disconnect the power cord before you service the
This section contains information designed to help you maintain the 432
Detector. Routine maintenance for the 432 Detector includes:
Replacing the fuse
Calibrating the detector
Maintaining the flow cell
Waters service specialists provide maintenance for the 432 Detector on a
corrective, as required, basis. Contact the Waters Technical Services
Department if you have questions regarding the repair or performance of your
instrument.
Follow these suggestions to help you maintain the 432 Detector:
Stock the recommended spare parts listed in Appendix B to reduce
downtime. Contact the Waters Service Department for assistance.
Record the initial installation date and serial number of your
instrument in for easy reference.
Keep a file of typical chromatograms for comparison when you suspect
Replacing the fuse
To change the operating voltage fuse:
1. Turn off the front panel power switch and remove the power cord from
its connector on the rear panel of the detector.
Warning: To avoid the possibility of electric shock, turn off the
front panel power switch, and unplug the power cord from the
2. Pry open the power connector cover with a screwdriver.
3. To change the AC power fuses, pull out each fuse holder as though
opening a drawer. Spare fuses are included in the System Startup Kit.
For ordering information, see
operating voltage fuses (for use in either North America or Europe).
5. Install the correct fuse in the holder and slide it back into place. The
arrow on each fuse holder points up when in the correct position.
Installing operating voltage fuses
6. Close the power connector cover. Then plug the power cord into its
connector on the rear panel of the detector.
Maintaining the flow cell
Maintenance for the 432 Detector consists of ensuring the flow cell is free of
foreign material. Foreign material in the flow cell may cause baseline drift,
cycling, or noise.
Caution: To avoid damaging the column, remove it before you flush the
system. Do not reconnect the column until the eluent has returned to
approximately pH 7.
To clean the cell:
1. Flush the system with ASTM Type I reagent water.
2. Flush the system with 20 mL of 6 N nitric acid (HNO3).
3. Flush the system again with ASTM Type I reagent water. Do not
reconnect the column until the eluent has returned to about pH 7.
Routine maintenance
Refer to , to order a replacement flow cell. The following tools are
required to replace the flow cell:
5/16-inch open-end wrench
Knife or flat-blade screwdriver
Warning: To avoid electrical hazards, always unplug the power cord
before you perform any of the following replacement procedures.
To replace the flow cell:
1. Unplug the 432 Detector from the power source, and completely
disconnect all electrical cables and fluid connections.
2. Remove the 432 Detector cover (four Phillips-head screws, two on each
3. Remove the two pins and pin holders that hold the cell block cover in
). Use a knife or
flat-blade screwdriver to gently pry the pins and holders out.
4. Pull off the cover of the flow cell unit and remove the top layer of
5. Remove the four Phillips-head screws from the upper plate of the cell
block, and remove the plate. Note the orientation of the plate: a notch is
cut into the underside to clear one of the components within the cell
6. Carefully disconnect the inlet and outlet fittings from the flow cell.
7. Remove the two Phillips-head screws from the flow cell mounting
8. Unplug the flow cell cable connector from its socket in the cell block.
9. Remove the flow cell assembly.
10. Install the new flow cell by following steps 2 through 9 in reverse order.
Be sure to orient the upper plate of the cell block properly before you
install the four screws.
Flow cell assembly
Upper plate screws
Cell mounting bracket screws
Routine maintenance
Cleaning the detector exterior
To clean the outside of the 432 Detector, use only a soft lint-free paper or cloth
dampened with mild soap and water.
This section contains troubleshooting charts to help you isolate and correct
problems with the 432 Detector.
Keep in mind that the source of apparent detector problems may lie within the
chromatography or hardware of your system. The Waters Guide to Successful
Operation of Your LC System contains detailed chromatographic
troubleshooting tables. (Contact your nearest Waters office for information on
how to get a copy.) If you cannot correct a problem, contact the Waters
Technical Services Department for assistance.
When you call Waters service
To expedite your request for service, have the following information available
when you call Waters regarding a 432 Detector problem:
Operating pressure
Base Range setting
Integrator Sensitivity setting
Recorder Sensitivity setting
Type of injector (automatic or manual)
Type of data integrator
Detector does not turn on
If your detector is completely inoperative (for example, the lights do not
illuminate and the display remains completely blank when the unit is turned
on), the fuse may require replacement. Refer
The 432 Detector performs startup diagnostics that check the internal
memory (both RAM and ROM), and the associated processing circuitry.
Power supply
The following factors can adversely affect the operation of the 432 Detector:
Transient energy sources
Be sure that the electrical supply used for the 432 Detector is properly
grounded and free from any of these conditions.
The error messages displayed by the 432 Detector are listed below along with
the recommended action for each:
ROM/RAM error (checked during startup only)
Call Waters service.
Check flow cell and associated plumbing connections.
Temperature control failure
Call Waters service.
Error: Over Range
Base over-range condition
Set Base Range to the next setting above the background conductivity
of the eluent.
Conductivity overflow (above 10,000 μS)
Dilute eluent to remain within measurable range.
Press the Clear key to clear an error alarm and message. For a continuing
error condition, the error message remains after the audio alarm is cleared.
To troubleshoot a problem:
1. Visually examine the integrity of the electrical and fluid connections as
you verify proper system configuration and installation.
2. If the results of previous runs are available, compare the current system
operation with the system operation before you identified the problem.
For example, if your system usually runs at a certain pressure with a
certain method:•
Is the system pressure in the same range, or is it drastically higher
(possibly caused by a blocked line) or lower (possibly caused by a
Are pressure fluctuations in the same range as during normal
3. Isolate the parameter that varies from normal operation. The
parameters to observe include:•
Peak retention time
Qualitative/quantitative chromatographic results
Evaluate the parameters in the order presented above to rule out simple
causes of the problem.
4. Refer to the to
determine corrective actions for the problems that you identify.
Bubbles in the flow cell are evident when the noise is equal to or greater than
2 μS. Use this method to remove bubbles.
To remove bubbles:
1. Disconnect the tubing from the inlet and outlet of the 432 Detector.
2. Attach a 1-mL tuberculin syringe to a priming syringe cannula which is
screwed into the inlet of the detector.
3. Flush four times with 1-mL portions of ASTM Type I reagent water.
4. Flush four times with 1-mL portions of HPLC-grade methanol.
5. Flush four times with 1-mL portions of ASTM Type I reagent water.
6. Reattach the tubing from the 432 Detector outlet to a waste receptacle
(18-inch length of 0.009-inch ID stainless steel).
7. Start eluent flowing through the system at a flow rate of at least 1
8. With the eluent flowing, reattach the detector inlet tubing to the
9. Allow a few minutes for temperature reequilibration, then check the
noise level. If it is not reduced, repeat steps 1 through 4, then proceed to
steps 10 through 13.
10. Attach a dead-end fitting to the 432 Detector outlet.
11. Remove the priming syringe cannula and attach a dead-end fitting to
the 432 Detector inlet.
12. Allow the detector to stand overnight (>12 hours) with temperature on
and with methanol in the flow cell.
13. Repeat steps 5 through 9.
Pulse dampener not
Check the pump; see
the pump manual.
Bubbles in flow cell
Remove bubbles and
degas the solvent.
Troubleshooting guide (Continued)
Voltage fluctuation
Spikes on baseline
Clean the cell.
Check flow cell fittings
and tighten. If leak
continues, replace the
Bubbles in flow cell
Remove bubbles and
degas the solvent.
Irregular noise on
Temperature changes
temperature, locate
drafts, and insulate
tubing and column, if
Cell temperature set
Set the cell temperature
lower than ambient
to a minimum of 5 °C
above ambient.
Replace the column.
Excessive baseline drift Unstable temperature
temperature control is
Defective cell heater
Call Waters service.
Temperature changes
temperature, locate
drafts, and insulate
tubing and column, if
Cell temperature set
Set the cell temperature
lower than ambient
to a minimum of 5 °C
above ambient.
Bubbles in flow cell
Remove bubbles and
degas the solvent.
Troubleshooting guide (Continued)
Excessive baseline drift Solvent changeover
Wait until baseline
stabilizes (purge
autosampler a few
Check flow cell fittings
and tighten. If leak
continues, replace the
Detector cannot be
Solvent changeover
Wait until the baseline
Bubbles in flow cell
Remove bubbles and
degas the solvent.
Continuous noise at
Pump crossover noise
high sensitivity (<1μS)
high-sensitivity noise
filter on the pump.
A Safety Advisories
Waters instruments display hazard symbols designed to alert you to the
hidden dangers of operating and maintaining the instruments. Their
corresponding user guides also include the hazard symbols, with
accompanying text statements describing the hazards and telling you
how to avoid them. This appendix presents all the safety symbols and
statements that apply to the entire line of Waters products.
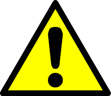
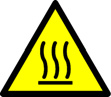
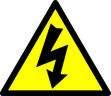
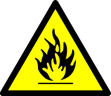
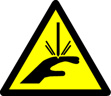
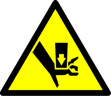
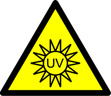
Warning symbols alert you to the risk of death, injury, or seriously adverse
physiological reactions associated with an instrument's use or misuse. Heed
all warnings when you install, repair, and operate Waters instruments.
Waters assumes no liability for the failure of those who install, repair, or
operate its instruments to comply with any safety precaution.
Task-specific hazard warnings
The following warning symbols alert you to risks that can arise when you
operate or maintain an instrument or instrument component. Such risks
include burn injuries, electric shocks, ultraviolet radiation exposures, and
others. When the following symbols appear in a manual's narratives or procedures,
their accompanying text identifies the specific risk and explains how to avoid
Warning: (General risk of danger. When this symbol appears on an
instrument, consult the instrument's user documentation for important
safety-related information before you use the instrument.)
Warning: (Risk of burn injury from contacting hot surfaces.)
Warning: (Risk of electric shock.)
Warning: (Risk of fire.)
Warning: (Risk of sharp-point puncture injury.)
Warning: (Risk of hand crush injury.)
Warning: (Risk of exposure to ultraviolet radiation.)
Warning: (Risk of contacting corrosive substances.)
Warning: (Risk of exposure to a toxic substance.)
Warning: (Risk of personal exposure to laser radiation.)
Safety Advisories
Warning: (Risk of exposure to biological agents that can pose a serious
Warning: (Risk of tipping.)
Warning: (Risk of explosion.)
Warning: (Risk of eye injury.)
The following warnings can appear in the user manuals of particular
instruments and on labels affixed to them or their component parts.
This warning applies to Waters instruments fitted with nonmetallic tubing.
Warning: Pressurized nonmetallic, or polymer, tubing can burst.
Observe these precautions when working around such tubing:• Wear eye protection.
• Extinguish all nearby flames.
• Do not use tubing that is, or has been, stressed or kinked.
• Do not expose nonmetallic tubing to incompatible compounds like
tetrahydrofuran (THF) and nitric or sulfuric acids.
• Be aware that some compounds, like methylene chloride and
dimethyl sulfoxide, can cause nonmetallic tubing to swell, which
significantly reduces the pressure at which the tubing can rupture.
Mass spectrometer flammable solvents warning
This warning applies to instruments operated with flammable solvents.
Warning: Where significant quantities of flammable solvents are
involved, a continuous flow of nitrogen into the ion source is required to
prevent possible ignition in that enclosed space. Ensure that the nitrogen supply pressure never falls below 690 kPa
(6.9 bar, 100 psi) during an analysis in which flammable solvents are
used. Also ensure a gas-fail connection is connected to the LC system so
that the LC solvent flow stops if the nitrogen supply fails.
Mass spectrometer shock hazard
This warning applies to all Waters mass spectrometers.
Warning: To avoid electric shock, do not remove the mass spectrometer's
protective panels. The components they cover are not user-serviceable.
This warning applies to certain instruments when they are in Operate mode.
Warning: High voltages can be present at certain external surfaces of
the mass spectrometer when the instrument is in Operate mode. To
avoid non-lethal electric shock, make sure the instrument is in Standby
mode before touching areas marked with this high voltage warning
Safety Advisories
This warning applies to Waters instruments that can be used to process
material that might contain biohazards: substances that contain biological
agents capable of producing harmful effects in humans.
Warning: Waters instruments and software can be used to analyze or
process potentially infectious human-sourced products, inactivated
microorganisms, and other biological materials. To avoid infection with
these agents, assume that all biological fluids are infectious, observe
Good Laboratory Practices, and consult your organization's biohazard
safety representative regarding their proper use and handling. Specific
precautions appear in the latest edition of the US National Institutes of
Health (NIH) publication, Biosafety in Microbiological and Biomedical
Chemical hazard warning
This warning applies to Waters instruments that can process corrosive, toxic,
flammable, or other types of hazardous material.
Warning: Waters instruments can be used to analyze or
process potentially hazardous substances. To avoid injury
with any of these materials, familiarize yourself with the
materials and their hazards, observe Good Laboratory
Practices (GLP), and consult your organization's safety
representative regarding proper use and handling.
Guidelines are provided in the latest edition of the National
Research Council's publication, Prudent Practices in the
Laboratory: Handling and Disposal of Chemicals.
The caution symbol signifies that an instrument's use or misuse can damage
the instrument or compromise a sample's integrity. The following symbol and
its associated statement are typical of the kind that alert you to the risk of
damaging the instrument or sample.
Caution: To avoid damage, do not use abrasives or solvents to clean the
instrument's case.
Warnings that apply to all Waters instruments
When operating this device, follow standard quality control procedures and
the equipment guidelines in this section.
Attention: Changes or modifications to this unit not expressly approved by the
party responsible for compliance could void the user's authority to operate the
Important: Toute modification sur cette unité n'ayant pas été expressément
approuvée par l'autorité responsable de la conformité à la réglementation peut
annuler le droit de l'utilisateur à exploiter l'équipement.
Achtung: Jedwede Änderungen oder Modifikationen an dem Gerät ohne die
ausdrückliche Genehmigung der für die ordnungsgemäße Funktionstüchtigkeit
verantwortlichen Personen kann zum Entzug der Bedienungsbefugnis des
Systems führen.
Avvertenza: qualsiasi modifica o alterazione apportata a questa unità e non
espressamente autorizzata dai responsabili per la conformità fa decadere il
diritto all'utilizzo dell'apparecchiatura da parte dell'utente.
Atencion: cualquier cambio o modificación efectuado en esta unidad que no
haya sido expresamente aprobado por la parte responsable del cumplimiento
puede anular la autorización del usuario para utilizar el equipo.
주의: 규정 준수를 책임지는 당사자의 명백한 승인 없이 이 장치를 개조 또는 변경할 경우,
이 장치를 운용할 수 있는 사용자 권한의 효력을 상실할 수 있습니다.
Safety Advisories
Warning: Use caution when working with any polymer tubing under pressure:
• Always wear eye protection when near pressurized polymer tubing.
• Extinguish all nearby flames.
• Do not use tubing that has been severely stressed or kinked.
• Do not use nonmetallic tubing with tetrahydrofuran (THF) or concentrated
nitric or sulfuric acids.
• Be aware that methylene chloride and dimethyl sulfoxide cause nonmetallic
tubing to swell, which greatly reduces the rupture pressure of the tubing.
Attention: Manipulez les tubes en polymère sous pression avec precaution:
• Portez systématiquement des lunettes de protection lorsque vous vous
trouvez à proximité de tubes en polymère pressurisés.
• Eteignez toute flamme se trouvant à proximité de l'instrument.
• Evitez d'utiliser des tubes sévèrement déformés ou endommagés.
• Evitez d'utiliser des tubes non métalliques avec du tétrahydrofurane (THF)
ou de l'acide sulfurique ou nitrique concentré.
• Sachez que le chlorure de méthylène et le diméthylesulfoxyde entraînent le
gonflement des tuyaux non métalliques, ce qui réduit considérablement leur
pression de rupture.
Vorsicht: Bei der Arbeit mit Polymerschläuchen unter Druck ist besondere
Vorsicht angebracht:• In der Nähe von unter Druck stehenden Polymerschläuchen stets
• Alle offenen Flammen in der Nähe löschen.
• Keine Schläuche verwenden, die stark geknickt oder überbeansprucht sind.
• Nichtmetallische Schläuche nicht für Tetrahydrofuran (THF) oder
konzentrierte Salpeter- oder Schwefelsäure verwenden.
• Durch Methylenchlorid und Dimethylsulfoxid können nichtmetallische
Schläuche quellen; dadurch wird der Berstdruck des Schlauches erheblich
Warnings that apply to all Waters instruments
Attenzione: fare attenzione quando si utilizzano tubi in materiale polimerico
sotto pressione:• Indossare sempre occhiali da lavoro protettivi nei pressi di tubi di polimero
• Spegnere tutte le fiamme vive nell'ambiente circostante.
• Non utilizzare tubi eccessivamente logorati o piegati.
• Non utilizzare tubi non metallici con tetraidrofurano (THF) o acido solforico
o nitrico concentrati.
• Tenere presente che il cloruro di metilene e il dimetilsolfossido provocano
rigonfiamenti nei tubi non metallici, riducendo notevolmente la pressione di
rottura dei tubi stessi.
Advertencia: se recomienda precaución cuando se trabaje con tubos de
polímero sometidos a presión:• El usuario deberá protegerse siempre los ojos cuando trabaje cerca de tubos
de polímero sometidos a presión.
• Si hubiera alguna llama las proximidades.
• No se debe trabajar con tubos que se hayan doblado o sometido a altas
• Es necesario utilizar tubos de metal cuando se trabaje con tetrahidrofurano
(THF) o ácidos nítrico o sulfúrico concentrados.
• Hay que tener en cuenta que el cloruro de metileno y el sulfóxido de dimetilo
dilatan los tubos no metálicos, lo que reduce la presión de ruptura de los
Safety Advisories
경고: 가압 폴리머 튜브로 작업할 경우에는 주의하십시오.
• 가압 폴리머 튜브 근처에서는 항상 보호 안경을 착용하십시오.
• 근처의 화기를 모두 끄십시오.
• 심하게 변형되거나 꼬인 튜브는 사용하지 마십시오.
• 비금속(Nonmetallic) 튜브를 테트라히드로푸란(Tetrahydrofuran: THF) 또는
농축 질산 또는 황산과 함께 사용하지 마십시오.
• 염화 메틸렌(Methylene chloride) 및 디메틸술폭시드(Dimethyl sulfoxide)는
비금속 튜브를 부풀려 튜브의 파열 압력을 크게 감소시킬 수 있으므로 유의하십시오.
Warnings that apply to all Waters instruments
Warning: The user shall be made aware that if the equipment is used in a
manner not specified by the manufacturer, the protection provided by the
equipment may be impaired.
Attention: L'utilisateur doit être informé que si le matériel est utilisé d'une
façon non spécifiée par le fabricant, la protection assurée par le matériel risque
Vorsicht: Der Benutzer wird darauf aufmerksam gemacht, dass bei
unsachgemäßer Verwenddung des Gerätes die eingebauten
Sicherheitseinrichtungen unter Umständen nicht ordnungsgemäß
Attenzione: si rende noto all'utente che l'eventuale utilizzo
dell'apparecchiatura secondo modalità non previste dal produttore può
compromettere la protezione offerta dall'apparecchiatura.
Advertencia: el usuario deberá saber que si el equipo se utiliza de forma
distinta a la especificada por el fabricante, las medidas de protección del equipo
podrían ser insuficientes.
경고: 제조업체가 명시하지 않은 방식으로 장비를 사용할 경우 장비가 제공하는 보호 수단이
제대로 작동하지 않을 수 있다는 점을 사용자에게 반드시 인식시켜야 합니다.
A-10 Safety Advisories
Warning: To protect against fire, replace fuses with those of the type
and rating printed on panels adjacent to instrument fuse covers.
Attention: pour éviter tout risque d'incendie, remplacez toujours les
fusibles par d'autres du type et de la puissance indiqués sur le panneau
à proximité du couvercle de la boite à fusible de l'instrument.
Vorsicht: Zum Schutz gegen Feuer die Sicherungen nur mit
Sicherungen ersetzen, deren Typ und Nennwert auf den Tafeln neben
den Sicherungsabdeckungen des Geräts gedruckt sind.
Attenzione: per garantire protezione contro gli incendi, sostituire i
fusibili con altri dello stesso tipo aventi le caratteristiche indicate sui
pannelli adiacenti alla copertura fusibili dello strumento.
Advertencia: Para evitar incendios, sustituir los fusibles por aquellos
del tipo y características impresos en los paneles adyacentes a las
cubiertas de los fusibles del instrumento.
경고: 화재의 위험을 막으려면 기기 퓨즈 커버에 가까운 패널에 인쇄된 것과 동일한
타입 및 정격의 제품으로 퓨즈를 교체하십시오.
Warnings that apply to all Waters instruments
Electrical and handling symbols
These can appear in instrument user manuals and on the instrument's front
or rear panels.
Electrical power on
Electrical power off
Alternating current
Protective conductor terminal
Frame, or chassis, terminal
Recycle symbol: Do not dispose in municipal waste.
A-12 Safety Advisories
These handling symbols and their associated text can appear on labels affixed
to the outer packaging of Waters instrument and component shipments.
Electrical and handling symbols
A-14 Safety Advisories
This appendix includes information on:
Less than 0.05 μS/hr/°C (ambient)Base: 200 μSSensitivity: 0.005Eluent: 1 mM KCI
Less than 0.005 μS/cmBase: 200 μSSensitivity: 0.005Eluent: 1 mM KCI
Temperature control Front-panel selectable: OFF, 30, 35, 40, 45, 50,
55, 60, 65 °CPerformance: 0.5 °C/hr
Fast: 0.25 secStandard: 0.5 secSlow: 1.0 sec
Mechanical specifications (Continued)
316 stainless steel, PTFE, and PCTFE
Operating pressure 70 psi maximumHeight
9.4 inches (23.8 cm)
21 inches (53.3 cm)
11.5 inches (29.2 cm)
17.7 pounds (8 kg)
Operating temperature range 4 to 35 °C
Operating humidity
20 to 80% RH, noncondensing
Protection classa
Over-voltage categoryb
Pollution degreec
Moisture protectiond
Line voltages (grounded AC), nominal 100/120 VAC
Line frequency ranges
50 Hz: ±2 Hz60 Hz: ±2 Hz
100/120 VAC fuse rating
220/240 VAC fuse rating
a. Protection Class I – The insulating scheme used in the instrument to protect
you from electrical shock. Class I identifies a single level of insulation between
live parts (wires) and exposed conductive parts (metal panels), in which the
exposed conductive parts are connected to a grounding system. In turn, this
grounding system is connected to the third pin (ground pin) on the electrical
power cord plug.
b. Over Voltage Category II – Pertains to instruments that receive their elec-
trical power from a local level such as an electrical wall outlet.
c. Pollution Degree 2 – A measure of pollution on electrical circuits, which may
produce a reduction of dielectric strength or surface resistivity. Degree 2 refers
to normally only nonconductive pollution. Occasionally, however, a temporary
conductivity caused by condensation must be expected.
d. Moisture Protection – Normal (IPXO) – IPXO means that there is NO
Ingress Protection against any type of dripping or sprayed water. The X is a
placeholder to identify protection against dust, if applicable.
Integrator output
10, 50, 100 μS/1V FS
Isolated contact output
IEEE-488, PowerLine™
C Spare Parts
The parts listed in the table below are spare parts recommended for
installation by you, the customer. Any parts that are not listed may require
installation by a trained service representative. Order a supply of the parts
listed below to keep in stock for use as needed.
Spare parts
Part number
Fuse, Time Delay, 1A, 250V, IEC
Fuse, Time Delay, 2A, 5x20 mm T
Pump Seal Replacement kit
Tip: The flow cell (part number 043069) is considered a replacement part.
Order the flow cell only when it is needed for replacement in the Waters 432
Detector.
Fill in the information below for easy reference when you order parts or
request service.
Installation Date: _
Serial Number:
D Ion Chromatography Methods
General anion analysis using conductivity and UV
Part number
Alliance, 2695 Separations Module or Breeze
(with column heater, seal wash, and degasser)432 Conductivity Detector
Empower/Breeze data processing
Common anion standards
IC-Pak A/HR (part number 026765)
Borate/gluconate containing 12% AcCN
Back conductivity
Ion Chromatography Methods
Analysis conditions (Continued)
30 °C for column heater, 35 °C for detector
12% AcCN in DI water
Direct conductivity
50 μS/Volt unattenuated
To prepare eluent:
1. Add 20 mL of lithium borate/gluconate concentrate and 120 mL of
HPLC-grade acetonitrile (AcCN) into a 1-liter volumetric flask (see
, for concentrate preparation).
2. Dilute to volume with DI water.
3. Ensure the natural pH is 8.2 ±0.1.
4. Vacuum degas through a 0.45-μm aqueous and solvent-compatible
membrane filter.
5. Store in a glass or plastic container at ambient temperature. Discard
after 1 month.
It is recommended that you use certified 1000-ppm anion standards with this
uncertified standard preparation.
Prepare at least three mixed analyte standards within the expected range of
sample analyte concentration. This method is linear from 0.1 to 100 ppm.
General anion analysis using conductivity and UV detection
After you validate the multi-point calibration curve, a single-point calibration
curve within the expected analyte concentration range is appropriate for
Preparing a sample
To prepare a sample:
1. Determine the expected range of analyte concentration and other
anionic component in the sample matrix. The major analyte should be
less than 100 ppm for best results.
2. Dilute the sample with DI water, if necessary.
3. If the sample contains high amounts of neutral organics or is highly
colored, pass the diluted sample through a C18 Sep-Pak cartridge.
Anions pass through unretained, but there can be a loss of fluoride
4. Filter samples containing suspended solids through a 0.45-μm
aqueous-compatible disk before injection. Failure to filter solids can
increase column backpressure.
Tip: For best results, ensure sample pH is between 3 and 11.
Samples treated with a sample preparation disk in the H+ form, used to
remove cations and neutralize high pH, will yield chromatograms
similar to suppressed conductivity chromatograms.
Ion Chromatography Methods
Empower data processing method
IC processing method using peak apex for retention time
Peak Width = 30.0Minimum Area = 3000Inhibit Intg. = 0 to 2 min.
Threshold = 10 to 25Minimum Height = 150
Averaging = NoneUpdate RT = NeverPeak Match = ClosestQuant By = Peak AreaFit Type = Linear for multi-point calibration, Linear
Through Zero for single-point calibration
Analyte NameAnalyte Retention TimePeak AreaAmounts
This validation design is abstracted from ASTM/EPA validation. It has been
used to validate all anion analysis methods. Many of the methods using this
General anion analysis using conductivity and UV detection
validation design are linear above 50 ppm.
Individual youden pair standard, in ppm
Calibration curves for chloride, fluoride, and bromide
Ion Chromatography Methods
Calibration curves for nitrite and nitrate
Calibration curves for sulfate and phosphate
General anion analysis using conductivity and UV detection
Quantitation Precision is the percent RSD of analyte peak area at each
concentration. Data is based on seven replicate injections of the validation
Ion Chromatography Methods
Method detection limits
Based on this representative chromatogram using a 100-μL injection, the
estimated detection limits, as ppb, at three times signal to noise (S/N) are as
Quantitation below these detection limits is not advised. You can obtain lower
detection limits using a 250-μL injection.
General anion analysis using conductivity and UV detection
The Certified Performance Evaluation Standards were diluted 1:100 with DI
water. Amounts are based on a multi-point calibration curve prepared from
Performance True Value 2.69
Evaluation
Official Anion Mean
Methods Wet
Chem & IC
Std DevAve IC n=3 2.63
±0.06 ±0.09 ±0.12
Alliance IC
0.975 1.014 1.001
Pak A/HR and
B/G Eluent
0.979 1.029 0.995
The Certified Performance Evaluation Standards were diluted 1:100 with
typical drinking water. Amounts are based on a multi-point calibration.
Drinking Water detected ±0.04
n=3, as ppm
Performance
D-10 Ion Chromatography Methods
Analyte recovery (Continued)
n=3; as ppm
% Recovery
Example of use
Typical drinking water, no dilution required
Using direct UV detection
Many anions are UV active in the range of 205 to 214 nm, such as NO2, Br,
and NO3, and the use of direct UV detection provides a degree of detector
selectivity. The
chromatogram of the anion standard that demonstrates this selectivity.
Generally, the lower the wavelength of detection, the greater is the response,
as seen with the difference between 205- and 214-nm chromatograms.
However, the borate/gluconate eluent has some UV absorption which causes
General anion analysis using conductivity and UV detection
negatives peaks at the retention time of the UV transparent anion, such as F,
Cl, PO4, and SO4, if present.
Direct UV detection
Direct UV detection is five times more responsive for nitrite and nitrate than
is conductivity detection and therefore provides lower detection limits. The
chromatogram in of a 100-ppb
anion standard demonstrates the improved sensitivity.
D-12 Ion Chromatography Methods
100-ppb anion standard
Waters 996 photodiode array detector
The borate/gluconate eluent has some UV absorption. Use of eluents that are
UV transparent, such as hydroxide and carbonate/bicarbonate, provide lower
detection limits.
Preparing lithium borate/gluconate 50X stock concentrate
To prepare lithium borate/gluconate 50X stock concentrate:
1. Using a 60-mL plastic syringe, add approximately 25 g of BioRad
AG-50W-X12 strong cation exchange resin in the hydrogen form, or
equivalent. Wash the resin with five 20-mL portions of DI water to
remove any ionic impurities from the resin. Discard the washings.
2. Dissolve 9.06 g of sodium gluconate in approximately 20-mL of DI water.
After dissolution, transfer this solution into the 60-mL syringe with
resin. Slowly pass this solution into a 1-liter volumetric flask. Wash the
resin with five 20-mL portions of DI water, then add the washing to the
volumetric flask. Discard the syringe and resin.
An alternative is to use commercially available 50% gluconic acid.
However, it comes as a brown solution that, when diluted, gives a yellow
tint to the eluent that can affect long-term performance. You can remove
the brown color by passing 5 mL of 50% gluconic acid through a C18
General anion analysis using conductivity and UV detection
Sep-Pak cartridge. This requires three Sep-Pak cartridges. Use 13.2 mL
of 50% gluconic acid for the eluent concentrate.
3. Adjust the volume in the flask to approximately 500 mL with DI water
and use a stirring bar. Add 7.2 g of lithium hydroxide monohydrate and
25.5 g of boric acid. With the aid of a magnetic stirrer, mix until all
reagents are dissolved.
4. Add 94 mL of 95% glycerol and mix. Remove the stirring bar and fill to
the mark with DI water.
5. Store this lithium borate/gluconate concentrate in a plastic container at
ambient temperature for up to 6 months. You can store it at 4 °C for up
to 1 year, but warm it to ambient temperature before use.
6. A white "string-like" material observed at the bottom of the container
indicates significant microbiological growth. If present, discard and
prepare again.
Preparing lithium borate/gluconate eluent
To prepare lithium borate/gluconate eluent:
1. In a 1-liter volumetric flask, add 20 mL of the 50X lithium
borate/gluconate concentrate and dissolve in 500 mL of DI water. Add
120 mL of HPLC-grade acetonitrile. Mix and fill to the mark with DI
2. Vacuum degas through a 0.45-μm aqueous / organic membrane.
The background conductivity of the lithium borate/gluconate eluent is
between 220 and 270 μS.
D-14 Ion Chromatography Methods
Alkali and alkaline earth cations, ammonium, and amines
Part number
Alliance, 2695 Separations Module or
Breeze (with column heater, seal wash, and
degasser)432 Conductivity Detector
Empower/Breeze data processing
3 mM HNO3/0.1 mM EDTA
Back conductivity
Alkali and alkaline earth cations, ammonium, and amines
Analysis conditions (Continued)
30 °C for column heater, 35 °C for detector
12% AcCN in DI water
Indirect conductivity
100 μS/Volt unattenuated
To prepare eluent:
1. Add 0.029 g of EDTA as the free acid into a 1-liter plastic volumetric
2. Dissolve in 500 mL of DI water with a stirring bar for 30 min.
3. Add 30 mL of 100 mM HNO3 (or 189 μL of concentrated HNO3).
4. Dilute to volume with DI water.
5. Vacuum degas through a 0.45-μm aqueous-compatible membrane to
remove excess EDTA crystals.
6. Store in a plastic container at ambient temperature. Discard after 1
It is recommended that you use certified 1000-ppm anion standards with this
uncertified standard preparation.
Prepare at least three mixed analyte standards, using plastic volumetric
flasks, within the expected range of the sample analyte concentration. This
D-16 Ion Chromatography Methods
method is linear from 0.05 to 20 ppm for lithium, sodium, and ammonium, and
0.05 to 50 ppm for potassium, magnesium, and calcium. Above these
concentrations, the response is off scale. After the multi-point calibration
curve is validated, a single-point calibration curve within the expected analyte
concentration is appropriate for future calibrations.
You can use this method for the analysis of Rb, Cs, Sr, and Ba.
Preparing a sample
To prepare a sample:
1. Determine the expected range of analyte concentration and other
anionic component in the sample matrix. Sodium should be less than
20-ppm for best results.
2. Dilute the sample with DI water, if necessary.
3. If the sample contains high amounts of neutral organics or is highly
colored, pass the diluted sample through a C18 Sep-Pak cartridge.
Cations pass through unretained. There can be residual Na
contamination from the cartridge.
4. Filter samples containing suspended solids through a 0.45-μm
aqueous-compatible disk before injection. Failure to filter solids can
increase column backpressure.
Tip: For best results, ensure sample pH is between 2 and 7 (especially
the alkaline earth cations). Samples with pH less than 10 are
appropriate for the alkali cations, ammonium, and amines.
5. For samples with pH less than 2, dilute the sample 1:10 with DI water
or treat the sample with an Alltech IC-OH cartridge to remove anions
and neutralize pH.
Alkali and alkaline earth cations, ammonium, and amines
Empower data processing method
IC processing method using peak apex for retention time
Peak Width = 30.0Minimum Area = 3000Inhibit Intg. = 0 to 2 min.
Threshold = 25 to 40Minimum Height = 500
Averaging = NoneUpdate RT = NeverPeak Match = ClosestQuant By = Peak AreaFit Type = Linear for multi-point calibration,
Linear Through Zero for single-point calibration
Analyte NameAnalyte Retention TimePeak AreaAmounts
D-18 Ion Chromatography Methods
Method detection limits
25-ppb cation standard
Based on this representative chromatogram using a 100-μL injection in a 2695
Separations Module, the estimated detection limits, as ppb, at three times
signal to noise (S/N) are as follows:
You can achieve lower detection limits by using a 250-μL injection.
Alkali and alkaline earth cations, ammonium, and amines
Examples of use
Typical drinking water, no dilution required
Typical municipal wastewater, diluted 1:50, overlay of duplicate injections
Tip: Alkyl and alkanol amine analysis standards are between 1 and 5 ppm, 3
mM HNO3/0.1 mM EDTA/3% AcCN.
D-20 Ion Chromatography Methods
Preparing stock reagent
Because it is difficult to prepare a stock eluent for this column, it is
recommended to prepare fresh working eluent.
To prepare stock reagent:
1. In a 1-liter plastic volumetric flask, add 0.029 g of EDTA (as the free
acid, not its salts) in 800 mL of DI water. Place on a magnetic stir plate
and stir for 10 minutes.
2. While stirring, add 189 μL of concentrated nitric acid and mix for 5
3. Remove the stirring bar and fill to the mark with DI water.
4. Filter through a 0.45-μm aqueous-compatible membrane filter before
use. There can be some remaining white crystals on the filter (EDTA).
This does not affect the performance of the eluent. Discard the filter.
Alkali and alkaline earth cations, ammonium, and amines
D-22 Ion Chromatography Methods
E Validation Support
Validation regulation overview
Federal regulatory codes require that instrumentation and automated
systems used for generation, measurement, and assessment of data undergo:
Operational qualification (performance verification) following repairs,
maintenance, and substantial periods of operation
Routine maintenance
Federal regulatory codes also require that laboratories maintain:
Written Standard Operating Procedures (SOPs) that indicate dates of
operational qualification and maintenance
Tip: Designate a person to be responsible for maintaining federally required
Waters regulatory compliance support
Waters provides a wide range of documentation and services to assist
customers in complying with the following areas of Standard Operating
Procedure regulatory requirements:
Instrument maintenance
Error messages, diagnostics, and tests
Instrument performance qualification (calibration)
Regulatory requirements regarding proper instruction for preparing,
programming, and operating the 432 Detector are satisfied by the Waters 432
Conductivity Detector Operator's Guide.
Validation Support
satisfies regulatory requirements for routine instrument
maintenance. includes:
Calibration adjustment
Replacing the flow cell
Summary of 432 Detector error messages
Troubleshooting tables
Additional Waters support
For more information about compliance support products and services, contact
Waters Technical Service Department.
Waters regulatory compliance support
Validation Support
PowerLine controller
audience and purpose
Containers, selecting and preparing
EC Authorized Representative
electrical symbols
anion, preparing
Beep-on-keystroke
cation, preparing
biohazard warning
general guidelines
Bubbles, removing
nitric acid, preparing
Bus LAC/E connections
Bus SAT/IN connections
equipment guidelines
Carbonate absorption, minimizing
flammable solvents
Chart recorder connections
Chart recorder offset
chemical hazard warning
Fluid connections
assembling fittings
Compression screw
making connections
Configuration, system
handling symbols
Bus SAT/IN to Bus LAC/E
Initialization self-test
sensitivity range multiplier
ISM classification
safety advisories
Sample preparation
Sensitivity Range key
Soda lime tube, using
Leak Alert output
cation, injecting
cation, preparing
mass spectrometer shock hazard
Millennium32 connections
Storage, long-term
Nitric acid eluent, preparing
Noisy baseline, troubleshooting
System configuration
Time constant, detector
Power requirements
cutting polymeric
PowerLine operation
purpose and audience
Unpacking the 432 Detector
Voltage, operating
Source: http://webclick-demo.co.il/forumsci/wp-content/uploads/2015/09/Principles-of-Conductivity-Detector.pdf
Our mission is to help the people of Canada maintain and improve their health. Health Canada Additional copies are available from: Telephone: (613) 954-5995 Fax: (613) 941-5366 This publication is also available on the Canada's Drug Strategy Division web site at the following address: It can be made available in/on computer diskette/large print/ audio cassette/braille, upon request.
Organización Meteorológica Comisión Oceanográfica Intergubernamental de la Grupo de cooperación sobre boyas de acopio de datos Poner freno a los actos de vandalismo perpetrados contra las boyas de acopio de datos Las boyas meteorológicas y oceanográficas, a la deriva o fondeadas, son esenciales para afinar nuestros conocimientos sobre los océanos. Miden datos como la presión atmosférica, la temperatura del aire, el viento o la temperatura del mar, no sólo en superficie sino también a diferentes niveles de profundidad (en algunos casos hasta los 500 metros) e, incluso, las boyas a la deriva miden también las corrientes marinas a partir de su trayectoria. Las medidas y las posiciones se transmiten por satélite en tiempo real a los centros meteorológicos y oceanográficos operativos.