Draft
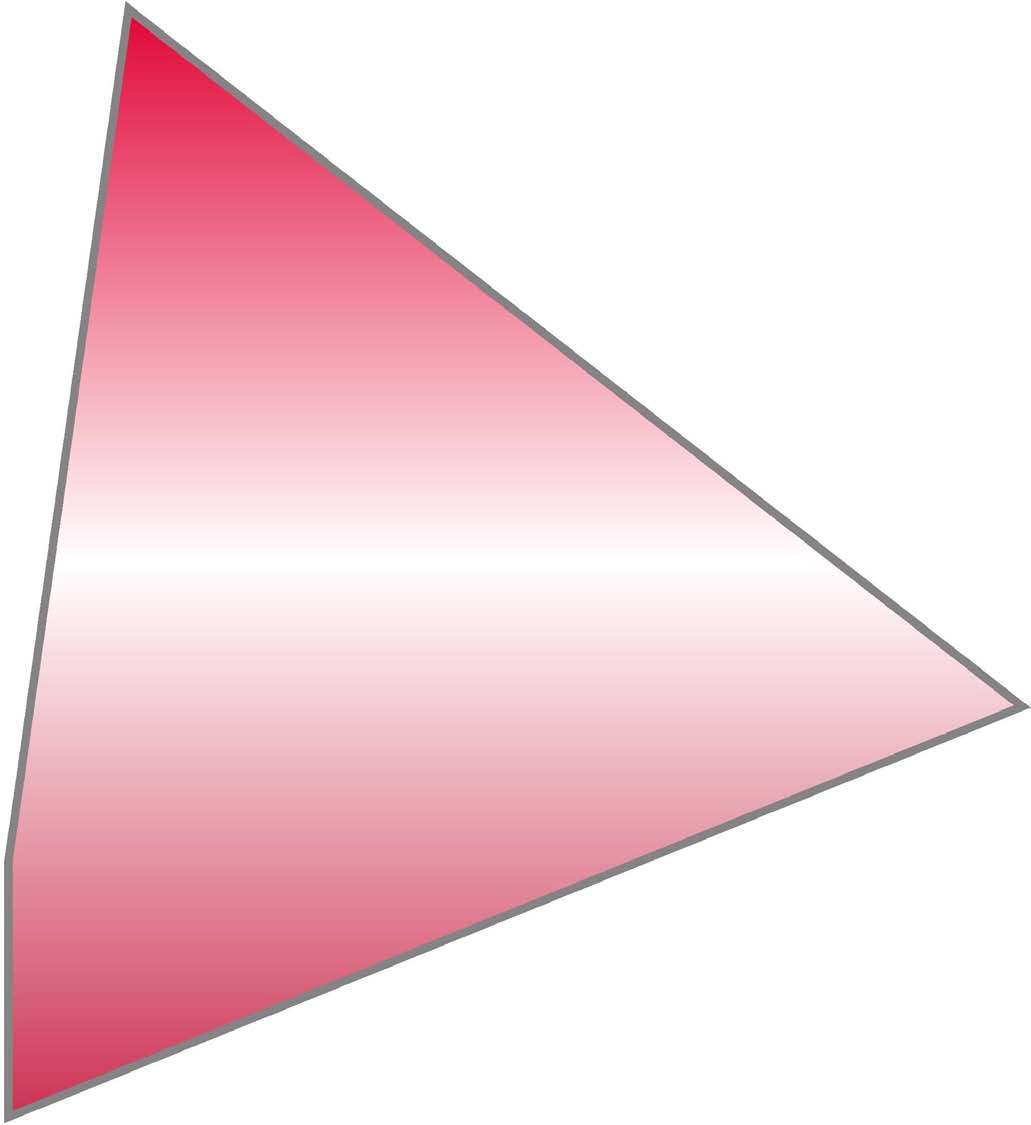
BIM Implementation:
An Owner's Guide to
Getting Started
CURT Owner Member Companies
Abbott Laboratories
Air Products & Chemicals, Inc.
The Procter & Gamble Company
Alstom Power, Inc.
Salt River Project
Shell Global Solutions (U.S.), Inc.
American Electric Power
Southern Companies
Barrick Gold Corporation
Baxter Healthcare Corporation
TECO Tampa Electric Company
Tennessee Valley Authority
Caterpillar Inc.
Tyco International
U.S. Architect of the Capitol
Constellation Energy
U.S. Army Corps Of Engineers
The Dow Chemical Company
U.S. Department of State
U.S. Federal Bureau of Prisons
U.S. General Services
Dynergy Generation
Eli Lilly and Company Exelon Corporation
ExxonMobil Chemical Company
Associate Member Companies
FirstEnergy Corporation General Electric Company
Aker Construction
Honda of America Mfg., Inc.
Intel Corporation
Johnson & Johnson
BMW Constructors
Linde Process Plants
EMCOR Group Inc.
The McGraw-Hill Companies
Fluor Corporation
Merck & Co., Inc.
Jacobs Engineering Group
Mirant Corporation
Rudolph/Libbe Companies
The Shaw Group, Inc.
Ontario Power Generation
Turner Construction Company
URS – Washington Division
Vulcan Industrial Contractors
Note: Membership listing current at time of publication
Association Associate Members
American Institute of Architects (AIA) American Institute of Steel Construction (AISC) Associated Builders and Contractors (ABC) Associated General Contractors of America (AGC) The Association of Union Constructors (TAUC) Design Build Institute of America (DBIA) Finishing Contractors Association (FCA) Mechanical Contractors Association of America (MCAA) National Association of Women in Construction (NAWIC) National Center for Construction Education and Research (NCCER) North American Contractors Association (NACA) National Electrical Contractors Association (NECA) Sheet Metal & Air Conditioning Contractors' National Association (SMACNA)
Copyright 2010 The Construction Users Roundtable. All rights reserved.
Notice: The purpose of this publication is to make available to industry the results of research and common owner practices. The information is provided solely for the individual consideration and education of The Construction Users Roundtable (CURT) members and the industry. The publication does not necessarily represent the views of every CURT member company on this topic. The booklet is offered as an informational publication only. CURT intends only to synthesize current thought and trends concerning the topic. Neither CURT nor its committees make any warranty as to the completeness of the materials. Readers are encouraged to further research the topic before relying exclusively on these materials. Each CURT member and other readers of these materials are free, acting in their own discretion and perception of business self-interest, to reject or adopt the recommendations in whole or in part. Adoption and/or reliance upon these recommendations are strictly voluntary.
The Mission of CURT is to promote cost effectiveness for owners doing business in the United States by providing aggressive leadership on issues that will significantly improve project engineering, maintenance, and construction processes, thereby creating value for the owners.
Note: Membership listing current at time of publication
BIM Implementation
An Owner's Guide to Getting Started
UP-1203, April 2010
Contents
Copyright 2010 The Construction Users Roundtable. All rights reserved.
Copyright 2010 The Construction Users Roundtable. All rights reserved.
1.0 Intent
This publication is for owners who want to implement Building Information Modeling (BIM). Because each project and each owner's enterprise is inherently different, there is no fully developed, off-the-shelf, one-size-fits-all solution for BIM implementation. This publication serves as a practical guide to help owners develop a BIM implementation process that best suits each owner's situation and needs. The paper is divided into three broad phases of project life cycle (Project Pre-Planning; Design & Construction; Operations & Maintenance) so that an owner can contemplate employing BIM processes at any time. In each phase, the publication follows a chronological process and provides both step-wise guidance on activities and key questions that owners need to ask themselves (and their team members) to ensure that the processes and desired outcomes realistically align with resources and capabilities. This publication is the product of the CURT Process Transformation Committee and has been developed with input and contributions from CURT members, architects, contractors, subcontractors, and fabricators, all with BIM experience. This group believes that owners have a unique opportunity to positively influence the adoption of BIM across the industry and continually improve the BIM implementation process.
Copyright 2010 The Construction Users Roundtable. All rights reserved
2.0 Initial Steps and Assessments
Assessment
Conduct an Internal Assessment to establish your intent and operation plan for BIM uses and implementation. The needs of every project and owner are different; there is no "one size fits all" approach to BIM. Understanding the specific outcomes required from a BIM affects the process and approach. Just as business models differ, so do BIMs.
Review your organization with objectivity, evaluate your
company's position and capabilities, and ask, "Is this organization set up to be successful with BIM?"
Consider willingness of personnel to embrace a different
type of project delivery and their tolerance for change. Success with BIM has direct relationships with the participants' level of determination.
Study current archiving and document control methods
in advance and compare them with expected BIM deliverables.
Determine the overall corporate focus for BIM. Is the
Lower total installed cost?
Produce better designs?
Assist with project budgeting and pricing?
Reduce claims or litigation?
Improve deliverable times?
Improve decision-making processes through better visualization and "what-if" scenarios?
Improve construction outcomes?
Prevent knowledge loss from construction to operations?
Create digital turnover documents?
Perform Operations and Maintenance?
All of the above?
Copyright 2010 The Construction Users Roundtable. All rights reserved
Answers to the above questions will assist the owner in forming an appropriate approach to BIM for various project types.
Focus on the high-value returns of BIM for your
business. Different project types and owners derive differing value from BIM. For instance, an owner with internal maintenance and operations staff may value life-cycle uses of the BIM more than an owner who does not. "Seventy percent of owners who adopt BIM as a standard method for construction delivery perceive a return on investment between ten and greater than one hundred percent."
Identify the internal champions to lead your BIM
implementation process.
Ensure that upper management is fully on board and
supportive of the process.
Consider your firm's willingness or ability to engage in
alternate forms of project delivery. The BIM process works best in a collaborative environment. Higher levels of communication improve outcomes. Some firms have limitations or legal constraints that preclude an integrated form of contract agreement, but a collaborative process can occur under any contract type.
Integrated project delivery (IPD) can exist independent of an integrated form of contract agreement. The National Institute of Building Sciences defines IPD as follows:
"A project delivery approach that integrates people,
systems, business structures, and practices into a
process that collaboratively harnesses the talents and
1 McGraw Hill 2009 SmartMarket Report, "The Business Value of BIM" http://www.nibs.org/index.php/bsa/newsevents/news/Entry/mcgrawhillconstructionsmartmarketreport2009
Copyright 2010 The Construction Users Roundtable. All rights reserved
insights of all participants to reduce waste and
optimize efficiency through all phases of design,
fabrication, and construction. Integrated Project
Delivery principles can be applied to a variety of
contractual arrangements and Integrated Project
Delivery teams will usually include members well
beyond the basic triad of owner, architect, and
contractor. At a minimum, though, an Integrated
Project includes tight collaboration between the
owner, the architect, and the general contractor
ultimately responsible for construction of the project,
from early design through project handover."
In its simplest form, IPD can be a non-contractual
agreement between parties to collaborate. An owner
who requires designers and constructors to reconcile
design documents with construction means and methods
to produce spatially coordinated installation documents
will achieve better outcomes, regardless of the contract
method used.
While the statements above might seem to contradict the traditional "arm's length" relationship between design and construction, traditional delivery methods have always included design review of installation shop drawings before construction begins. An integrated approach improves collaboration and communication; reduces cost-bearing requests for information (RFIs); and improves outcomes.
2 See Integrated Project Delivery — A Working Definition http://www.ipd-ca.net/images/Integrated%20Project%20Delivery%20Definition.pdf
Copyright 2010 The Construction Users Roundtable. All rights reserved
Consider the project funding and cash-flow differences
Creating a spatially accurate, constructible BIM requires more effort earlier in the design process but less during construction administration. Design and collaboration fee structures may need to be modified to reflect this effort.
If a traditional Design – Bid – Build model is employed, additional time and cost is required for completion of spatial coordination and construction installation drawings after bid and before construction. It is currently unrealistic to assume designers will include all aspects required for construction in a Design – Bid – Build delivery process, because stakeholders will be missing during the design process (i.e., mechanical, electrical, plumbing, and fire protection). Competitive pricing for equipment, material, and joining method selections is one of the key components specialty contractors provide to the value stream of a project. A project that uses BIM can expect lower final installed cost; fewer RFIs and change orders related to spatial interferences; and reduced risk of litigation related to interpretation of design intent.
Consider the legal implications of BIM.
BIM contracts often differ from traditional contracting methods and may require review by legal and surety insurance personnel to ensure compliance with corporate requirements. When encouraging collaboration and sharing of data between parties, limitations of liability among participants becomes an issue. Communicating the intended purpose for data and its integrity at the time of exchange improves the understanding of how to use the information.
Copyright 2010 The Construction Users Roundtable. All rights reserved
3.0 Project Pre-Planning
Project pre-planning has long been the cornerstone of effective project execution. This essential step continues to be paramount for successful implementation and use of BIM on a project. This section outlines key areas for consideration, frames questions within each area to assist in internal implementation, and assists in establishing a specific plan for BIM uses and implementation.
Technology Capabilities
Software and Interoperability
Decide between a proprietary software format and an open standard. Some owners have a great deal of legacy data in formats that must be maintained, while others are more willing to accept an open standard deliverable such as the Industry Foundation Class (IFC); each has certain benefits and detriments.
An open standard, if acceptable, will result in a greater ability to maintain data accessibility over time. Mandating a proprietary single software solution may limit the number of qualified designers and contractors but improve internal post-construction data use.
Selection of proprietary solutions reduces data accessibility as the solution provider (software developer) makes future version changes, or files format changes.
Sustainability and retrieval of digital information over time is an imperative to life-cycle uses of BIM. Software programs come and go and so do digital file formats. For digital data to remain retrievable over time, procedures for archiving and updating must be in place.
3See: Sustainability of Digital Formats http://www.digitalpreservation.gov/formats/sustain/sustain.shtml
Copyright 2010 The Construction Users Roundtable. All rights reserved
Internal Qualifications, Training and Education
Ensure that you have adequate qualified personnel proficient in the use of the selected BIM technology if you will use internal resources during the design and construction phase, or use the BIM for operations and maintenance. Consider training internal staff members or accessing consulting firms to fill roles if needed.
Information Technology Considerations
BIM requires a high level of information technology support and buy-in. Ensure that the IT manager is involved and willing to assist when necessary.
Do you have an IT structure for file management beyond the project timeline? If so, does the output allow for easy adoption or adaptation to BIM data?
Is BIM adoption the driver for developing a new file management structure? The Building Information Model contains a large amount of valuable data. Post-construction data retrieval is more efficient if an organized system is in place during its creation.
The BIM Execution Plan
Developing rationales and value propositions for a BIM on a project is important. Collaborating parties must define how a model is developed, and how the information produced will be used. Stakeholders have different information needs throughout the design, construct, and operate cycles of a facility. To this end, a properly planned BIM execution plan can be of great assistance.
The BIM execution plan is a strategic and tactical tool to plan the social interactions of the BIM team from the period before engagement, through design and construction. It is also a valuable tool to assist with post-construction information handoff.
4 See: Project Execution Planning Guide: http://www.engr.psu.edu/ae/cic/bimex/-
Copyright 2010 The Construction Users Roundtable. All rights reserved
If your firm will be involved with the technical aspect of
the BIM process, consider the following:
o Do you have adequate trained staff for the task? o What (if any) outside resources will you rely on? o Who will manage the data at each stage? o What is the final deliverable? o How will information be used after construction? o Where will it reside? o Who will maintain it? Listed below are some processes that benefit from a BIM-enabled project delivery method and may assist with answering the questions above.
o Enterprise planning o Project planning o Programming o Proof of performance o Consideration of design alternatives o Cost and schedule evaluation o Visualization studies o Permitting o Design and construction o Sales and leasing o Commissioning o Portfolio management o Tennant build-out o Future building additions and alterations o Facility Management
To assist in reducing the number of variables and
defining roles, responsibilities, and deliverables, a BIM execution plan is a key component of success. The graphic below (Figure 1) is a sample matrix used to define roles at various points along the project timeline.
Copyright 2010 The Construction Users Roundtable. All rights reserved
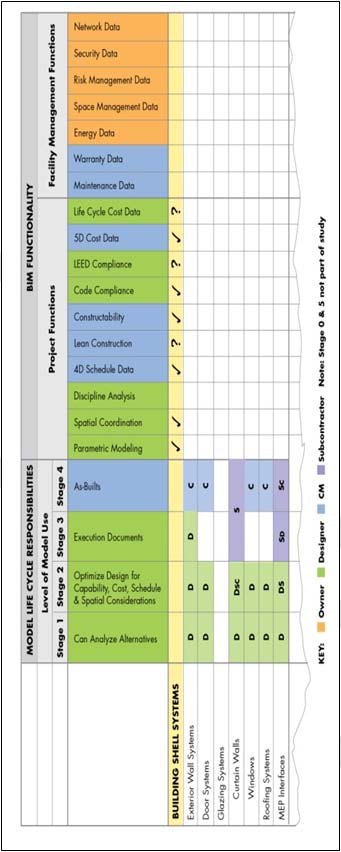
Figure 1: BIM Roles and Responsibilities
Copyright 2010 The Construction Users Roundtable. All rights reserved
Consider the following for inclusion in your BIM execution plan:
Portfolio management group spatial planning and programming enabled with a BIM.
Scenario-based planning and implementation.
Space utilization, phasing plans, etc.
Enterprise financial area / purpose, other business lines.
Responsibilities.
Information handoff.
Reliance on data at certain stages.
Project Team Selection
Assembling the right team is essential in project pre-planning, especially on projects using BIM. Considerations of market, skill sets, appropriate requests for qualifications (RFQs), and requests for proposals (RFPs), as well as accurate definition of BIM scope, are factors to consider.
Potential Participants
Consider your market. Analyze availability of qualified potential team members within the project locale, and assess the technical maturity of the region. This knowledge may influence the information entered in or produced from the model.
Is the BIM expertise you'll require to achieve your desired implementation strategies and goals available in your geographical area / region? If not, can you acquire it effectively elsewhere? Some regions have talent available on a consulting basis that can provide expertise where needed.
Copyright 2010 The Construction Users Roundtable. All rights reserved
How will the design team, construction team, consultants, and subcontractors embrace the use of BIM? Are their attitudes about BIM aligned with your project and company goals? Positive, "can-do" attitudes ensure success, whereas reluctant partners may try to prove BIM does not work.
Are your existing project consultants and constructors BIM capable? If they have not used BIM, are they willing and able to transition to a BIM process? If they have been contemplating a move to BIM, their enthusiasm may help foster project success.
Will you consider exploring new relationships with new team members who have demonstrated BIM expertise?
"BIM users would rather work with strangers who know BIM than with friends who don't. A majority of users (between 55% and 74%, depending on the discipline) gave high value to other team members on a project having BIM experience. This displaces the traditional favorite, ‘previous experience working together,' which scored only 42%. Additionally, when asked to rate factors that would most enable improved ROI, 66% of BIM users gave a high score to ‘more external firms with BIM skills.' This shows that adoption needs to accelerate to meet demand."
Developing the RFQ / RFP
It is critical that the owner develop a clear understanding of potential team members' experience with BIM. Determine whether they have proven experience or merely a BIM-for-marketing (BIM Wash) presentation. Careful review of experience and qualifications, along with a well-written RFQ, will clarify the respondent's capabilities and qualifications. Below are some sample questions to ask yourself and prospective RFP recipients.
5 McGraw Hill 2009 SmartMarket Report, "The Business Value of BIM"
Copyright 2010 The Construction Users Roundtable. All rights reserved
The RFP should clearly reflect your BIM goals and intent and should communicate your expectations of the BIM team. It must focus on the necessary skills and processes required for successful BIM implementation. A focus on value-added vs. first cost is strongly recommended (see CURT WP 1003 for more information regarding costs.) A best-value analysis will guide an owner through the process of defining the roles, responsibilities, and capability requirements for collaboration partners.
The RFP should outline performance metrics for the project and define exactly how success is measured. Consider the following metrics and goals:
o Alignment with your business corporate metrics
o Milestone dates
o Safety expectations
o Sustainability goals (energy performance, rating
system compliance, etc.)
o Number of RFIs and change orders
o Definition of value and measurement of achievement
Qualifying Questions for Potential Participants
To what extent does your company use BIM for
o Scenario-based planning and implementation o Space utilization, phasing plans, etc. o Visualization (three-dimensional enhanced
understanding of design proposals, ability to see design in context, etc.)
o Spatial coordination (three-dimensional coordination
between engineering disciplines and construction trades during the design phase)
6 CURT WP 1003 Construction Strategy: Optimizing the Construction Process
http://www.curt.org/14_0_curt_publications.html
Copyright 2010 The Construction Users Roundtable. All rights reserved
o Quantity take-offs (greater accuracies in material
quantity estimates)
o Linkage to in-house estimating systems and
o Cost estimating (four-dimensional — direct
connection between cost data and material quantities improves quality of estimates)
o Construction scheduling / coordination (five-
dimensional — improved construction staging and sequencing planning)
o Construction stage information shop review, creation
of record documents
o Prefabrication (use of model for off- or on-site
prefabrication improves quality and efficiency and reduces material waste)
Has your company completed one or more BIM
What are the specific details of your BIM projects
(dollar value, size, type, etc.)?
Did other parties on the project(s) also use BIM? If so,
how effectively? If not, why not?
Have you shared models with other stakeholders? If so,
have you experienced benefits or pitfalls because of model sharing?
Have you worked in a collaborative or integrated process
on projects? If so, what was your experience?
What software packages do you have experience with or
typically use? How do you use them?
How has BIM changed or affected your process?
What is your next developmental area in the use of
Defining the BIM Scope
Define the specific deliverables for the project, the
information to be included, the form, when will it be provided, by whom, and to whom.
Copyright 2010 The Construction Users Roundtable. All rights reserved
Align the desired information to support your current
business model. Ask, "Do you want to try to ‘push the envelope' with new information technologies and capabilities?"
Could the desired information support your future
business model expectations? A Building Information Model can support long-term facility life-cycle goals.
Establish the minimum requirements and expectations of
the model, the "must-haves"?
Are there other requirements and expectations of the
model? "Nice-to-haves?" Sometimes the "nice-to-haves" come as part of the process and incur no additional effort. (It never hurts to ask.)
Monitoring Metrics
Decide how often and when you will assess performance
of the project's team.
Establish metrics for measuring project success during the project pre-planning stage. Monitor regularly against project goals and traditional delivery methods. Suggested metrics include milestone dates, improved safety, performance goals, sustainability outcomes, RFIs,change orders, value, schedule, budget, and other measures deemed valuable to the project team.
Contracting of Team Members
Based on responses to the RFQ, assemble a preliminary project team consisting at minimum of a design team and a prime contractor. Your procurement team, with the design team and prime contractor, will work together to strike an appropriate balance for the project in terms of selecting the remaining early team members (how and when you bring in team members, what skills they must bring to the table, how and when competition will be established, etc.).
Copyright 2010 The Construction Users Roundtable. All rights reserved
Create Team Strategy
Are your proposed designers and contractors experienced and able to deliver a BIM that meets your requirement? If you have not defined your requirements, it is difficult to answer this question. Selection of qualified team members is essential.
Determine how comprehensive you want the early team
member selections to be and when to bring them on board. (Early inclusion of consultants, subcontractors, specialty trades, major suppliers, etc., may result in reduction of redundant work, better budgetary feedback, and earlier material and equipment selection).
Will the pursuit of competition help or hinder the process and project? Competitive pricing that allows for early selection can be obtained through scenario-based requests for quotation, fixed-profit arrangements, or fee-for-service proposals.
Mitigate risk associated with early selection. Low- or
non-performing team members can stall the BIM process, and an owner should have "escape clauses" for participants who fail to meet budgetary or time commitments.
What is the best time to lock in particular responsibilities
for the project? A good pre-plan will reveal best timing for selection.
Decide who the major subcontractors should be. What
information is needed from them, and when? Consider when they will be needed in the development of the project and whether they will provide the greatest value. Selecting too early does not necessarily add value, and selecting too late can be cause for missed opportunities.
Determine who must be BIM-savvy vs. BIM-conversant,
which participants (or companies) need to have a full grasp of your intended goals, and which companies can act in a supporting role.
7 See: Arizona Revised Statutes §34-or one State's
solution.
Copyright 2010 The Construction Users Roundtable. All rights reserved
The project team must understand and accept the
benefits of BIM implementation and not be reluctant participants.
Consider bringing BIM novices or tangential players to
the project team and pursue buy-in. Some recent converts to BIM can offer a lot to the team by way of new and creative ideas and enthusiasm.
Assign Roles and Responsibilities
With the primary participants in place and a strategy established, the expanded team should address issues that lie ahead with the resources they bring to the group. Consider using such resources as the Associated General Contractors' ConsensusDOCS BIM Addendum or the American Institute of Architects' (AIA) E202 BIM Protocol Exhibit to assist with aligning key responsibilities with the talent at hand.
In most cases, the roles and responsibilities of the parties in a BIM process are no different from those of traditional delivery processes. The big difference is the effort required by the team members to produce, manage, and deliver more detailed, precise, and accurate information.
Assign an information manager (the person who will
manage model and other project data). This can often be someone on the project team who has good leadership and communication skills. It may be appropriate to change leaders at different stages of a project. Design, Bid, Build will differ from integrated forms of agreement, for example.
Contract Documents and Language
Having developed criteria, put in place a strategy, and conducted a best-value selection, you are ready to engage a team that will collaborate to optimize BIM use. Next, develop a revised proposal to
8 AGC ConsensusDOCS 301, BIM Addendum www.agc.org/galleries/contracts/ConsensusDOCS%2520301%2520BIM%2520Addendum%2520Article.pdf 9AIA E202, BIM Protocol Exhibit http://info.aia.org/aia/form_free_bim.cfm
Copyright 2010 The Construction Users Roundtable. All rights reserved
reflect the selected team's strengths and skill sets and confirm with the selected team.
Confirm with your internal legal staff the proposed BIM process and the requisite information flow to achieve its benefits. Ensure there are resources available to your legal staff to address concerns and seek clarifications as necessary.
Do your existing Contract Form(s) allow for implementing the principles set forth in this document, and are they aligned with your BIM tactical and strategic goals? Are you modifying forms for this contact? If so, do you have a process in place to solicit feedback and implement concurrent change if appropriate?
If you are using specialized procurement processes such as Design Assist, do you have contractual language to address the nuances of process and information flow from the model? Are all parties to the project aligned?
Clearly outline your BIM strategy for this particular project in the contract. Include a background note on your corporate BIM strategy and a list of potential "targets of opportunity."
Once established, how does the contract address the need to grow and / or expand the team? How do you bring on new members? Does the project team understand this? Who has a say in this action? Is there a process set up to make this a seamless action?
Consider incentives tied to achieving BIM development milestones and goals.
Upon successful negotiations, execute the contract.
Copyright 2010 The Construction Users Roundtable. All rights reserved
Finalize the BIM Execution Plan
Synchronize the BIM process with funding /cash flow
Establish project funding and cash flows during the project milestone scheduling process, to understand when costs will be incurred and how to fund them.
This approach differs from conventional delivery methods in that more resource effort is expended earlier in the process to ensure a greater efficiency during construction.
Determine how budget assessments and cost controls are maintained. As the design and scope evolve from concept to construction, ongoing budgeting and cost analysis should be required to ensure that project costs stay within the parameters of the initial business case. If design precedes construction, guaranteed maximum price (GMP) or lump-sum costing is possible. This may require that certain key subcontractors be selected early in the design phase.
Set up an effective management framework.
Establish process checkpoints and metrics for regular measurement and assessment to ensure compliance with budgetary, schedule, and quality considerations. Establish and monitor milestone dates for design decisions, submittals, approvals, and deliverables.
Establish design "freeze points" to allow time for spatial coordination and administrative review prior to start of construction processes.
Determine how often to update the BIM (during construction, after construction, during facility life cycle, etc.).
Improve efficiencies of delivery. Designers and contractors should be encouraged to eliminate redundant work processes through close collaboration. Re-definition of traditional delivery roles could be required.
The decision-making process should be open, collaborative, and timely. The process may result
Copyright 2010 The Construction Users Roundtable. All rights reserved
in development of shop-drawing level of detail models during the traditional design phases of the project. Make decisions earlier in the process to allow timely completion of design with spatial coordination.
Milestones for major materials and equipment selections and manufacturer-specific components should occur early in the deliverables schedule to allow propagation of the information model with dimensionally accurate components. This will also facilitate early order of long lead-time materials.
o All parties must agree in advance on how to handle
field changes. Incorporate all field changes into the BIM before project completion and include with the project turnover package.
o Establish specific performance metrics for the
project that are consistent with those outlined in the RFP and the capabilities of the team players. Define exactly how success is measured.
Concurrent Learning
BIM is an evolving tool. It is paramount to have a process in place to capture lessons learned during and upon completion of the project. Open communication is essential. Strive for concurrent learning akin to a research and development environment, and continuously feed this information back into the system.
"72% of [BIM] users who formally measure their ROI report positive returns compared to 53% of users who estimate…"
10 McGraw Hill 2009 SmartMarket Report, "The Business Value of BIM"
Copyright 2010 The Construction Users Roundtable. All rights reserved
BIM Without Early Contractor Involvement
If certain contractors and subcontractors are not selected early on a fee and qualifications basis, determine how and when key players will be brought on board and prepare for redundant efforts that may take place during the design and construction of the project.
Design coordination efforts with design intent models may not guarantee that all components and systems are in place and ready for construction.
Reliance on the Model(s) — Will the model be a contract deliverable to be relied upon by the construction team for downstream use? o Models issued "for supplemental purposes only"
require the construction team to recreate construction-specific models.
o Does the model contain information that is useable
and useful to the construction team?
o Does the model contain key information for the
construction team? If not, it is helpful to identify the areas where information is lacking.
o To what degree is the model dimensionally and
geometrically accurate? This must be clear to the construction team to allow them to determine the work required to create construction phase models.
o Before releasing models for downstream use by the
construction team, determine to whom and for what purpose they will be conveyed.
o Incomplete or inaccurate models have some value to
the construction team, provided that the inaccurate or missing information is communicated adequately.
Project Pre-Planning Summary
The project pre-planning process is complex and complicated, but the value and ROI of having a well-planned process before engaging stakeholders are well worth the effort.
Copyright 2010 The Construction Users Roundtable. All rights reserved
Building Information Modeling achieves best outcomes through a collaborative process between owners, designers, and contractors (both general and specialty.) If a traditional Design, Bid, Build form of contracting is required, contract language should include a requirement that parties collaborate.
4.0 Design and Construction
Integrating the design and construction process using BIM reduces redundant work processes through close collaboration and workflow sharing between the design and construction teams. This is a major departure from traditional delivery methods where each party historically produced a work product in a closed environment and then handed it off to other stakeholders. Each party participates to their highest level of expertise. Designers may provide conceptual and spatial information to constructors who then add constructability analysis and information to the process. Regardless of project delivery process, designers retain responsibility and control of the design, and contractors retain responsibility and risk for construction means and methods.
"BIM facilitates leaner construction processes that directly impact the way subcontractors and fabricators work in four ways:
Greater degrees of prefabrication…
Improved workflow stability
Enhanced teamwork…
o Reduced inventories of engineered-to-order
(ETO) components"
11 BIM Handbook: A Guide to Building Information Modeling (Eastman, Teicholz, Sacks, and Liston) ISBN: 978-0-470-18528-5
Copyright 2010 The Construction Users Roundtable. All rights reserved
Monitoring Consultants
Consultants (both design and pre-construction) should be bound by metrics established in the BIM Execution Plan and monitored closely to avoid unexpected cost overruns or delays due to indecisiveness about design changes. Establish measurable accountability and defined calendar deadlines as early as possible. "Freeze points" for decisions and deliverables assist in timely design completion and reduce the tendency to "polish the apple." Solicit budgetary feedback from the affected installing contractors at each major design decision to review for cost implications.
Model Creation
Determine if the project will have a Federated or an
Integrated modeling approach.
The "Federated Model" concept requires that all component models be combined for coordination only; each model creator retains responsibility and ownership for their model and work. Component models are updated by their respective creators and combined for coordination as the project moves forward.
The "Integrated Model" concept requires that all component models exist in one model, with one entity responsible for maintaining the integrated model. The integrated model becomes better and better defined as the project moves forward. A designated party will be responsible for the integrated model.
Create a schedule for critical design decisions and
establish freeze points that support construction milestones.
Manage design changes and prevent unlimited
scenario analysis.
Determine whether third parties (end users;
consultants; major suppliers; government,
Copyright 2010 The Construction Users Roundtable. All rights reserved
regulatory, municipal agencies; etc.) will be engaged.
Schedule when models are released for downstream
Establish the needs for 2D paper deliverables.
Require that 2D deliverables be extracted from the 3D BIM.
Determine what supplemental drawings or typical
details are not in the model, where they exist on the project, and how this information will be conveyed to the installation team.
Determine uses of the information in the model
Who will use it and for what purpose?
Where will the BIM reside? Will the model (and appropriate support) reside on the project site? Owners and the project team should decide if the BIM will be used on the job site during physical project construction. If models will be used during construction, owners should require that the BIM(s) be used throughout the design, construction, and commissioning process. Insisting on accuracy of information within the model will ensure accurate turnover data and its suitability of use for future projects, facility services, etc.
Owners should decide on their final and best uses of the BIM at project inception. Graphical and non-graphical information may have equal or lesser value, depending on when the information is accessed. Do not be afraid to ask for what you think you need (in many cases, the data may be available without additional cost if requested early).
Existing technology provides the end user with many means for accessing project data. Careful thought and consideration at the beginning of the project prevents excessive data entry late in the process.
Decisions regarding how the end user(s) will need to interact with the information model should influence the final deliverable and formats for data access.
Levels of Detail
Copyright 2010 The Construction Users Roundtable. All rights reserved
Require levels of detail appropriate for the intended use of the information. A model used for square foot quantity take-offs requires much less detail than a model required for shop fabrication.
Cost andscope models
Cost and scope models should include general information on big-picture items such as floor area, use designations, building volume, and building grids. These models may not necessarily need to be used throughout the entire project.
Conceptual Design Models
Conceptual models should contain some major design elements and systems, but do not need to be highly developed.
Scheduling Models
Scheduling models need enough detail and granularity to allow separation of the model into discrete construction sequences.
Bidding Models
Bidding models contain overall geometry and design requirements of systems, but may not be highly detailed.
Construction Models
Construction models have the highest level of detail on a project. They contain the "means and methods" to construct the systems and components of the building. Construction models are used for shop-drawing production, fabrication, submittal for compliance of design intent, permits, etc.
As-Built Models
As-built models are useful as record models of the completed structure and may be required by the operations and maintenance (O&M) staff for managing the building over its life cycle.
BIM considerations during design and construction
Copyright 2010 The Construction Users Roundtable. All rights reserved
Not all parties involved with the project may be willing or able to engage in the more integrated design and construction processes necessary to maximize the value of BIM. Some less-critical participants may engage in a more traditional design and construction practice. The General Contractor or Construction Manager will coordinate this work in a way that minimizes impact to the process. One or more of the early team participants might be required to model or add information for the non-participating party. As an example, the structural steel system and mechanical, electrical, and plumbing (MEP) systems may be developed in an integrated fashion to facilitate spatial coordination, while metal stud and drywall systems may be delivered by more traditional means. In this example, one of the fully engaged team members would model components required to ensure accurate spatial coordination.
Spatial coordination
Accurate construction-level detail modeled by all major space consumers is required to complete spatial coordination. Early design-level attempts can allocate space for building components, but until all systems are integrated into the structure with dimensionally accurate installation level components, there is no certainty of outcome.
"Regardless of the model's accuracy, the contractor must ensure that the building is modeled with an appropriate level of detail. It must have sufficient details for piping, ducts, structural steel and attachments, and other components (electrical systems, fire protection piping, and seismic bracing), so that clashes can be accurately detected."
12 BIM Handbook: A Guide to Building Information Modeling (Eastman, Teicholz, Sacks, and Liston) ISBN: 978-0-470-18528-5
Copyright 2010 The Construction Users Roundtable. All rights reserved
Trade-Level Detail Models
Trade-level detail models ensure construction level accuracy. The process works best when the entity creating the model is responsible for installation. Turnover and spatial coordination requirements determine the level of detail required. Below is an excerpt from the BIM Forum "MEP Spatial Coordination Requirements for Building Information Modeling" that depicts the minimum level of detail required for spatial coordination and order of precedence for installation of non-modeled components.
Major Components
Heating, Ventilation, and Air Conditioning (HVAC) Duct — All ductwork, grilles, registers, diffusers, dampers, access panels, air-moving equipment, maintenance clearances, and any item that may impact coordination with other disciplines.
HVAC Piping — All overhead piping, vertical piping in shafts, connections to equipment, scheduled equipment, maintenance clearances, hangers, supports, and any item that may affect coordination with other disciplines.
Plumbing — All overhead piping, vertical piping between floors, connections to equipment and fixtures, maintenance clearances, hangers, supports, and any item that may affect coordination with other disciplines.
Fire Protection Piping — All overhead piping, branch connections, drops and heads, access panels, maintenance clearances, hangers, supports, and any item that may impact coordination with other disciplines.
13 AGC BIM Forum MEP Spatial Coordination Requirements for Building Information Modeling.
Copyright 2010 The Construction Users Roundtable. All rights reserved
Electrical — All conduits 2 inches and larger, any rack of two or more conduits regardless of size, lights and fixtures, electrical pull and circuit boxes, access clearances, all cable trays, hangers, supports, raceways, and any item that may impact coordination with other disciplines.
Framing —- All king studs, headers, and any item that may affect coordination with other disciplines.
"After all coordinated components are in place, installation of items not included in the coordinated installation drawing may begin. Any items not in the coordinated model will be installed after coordinated items are in place. Accessibility to install non-coordinated work is not an exclusion or exception to this requirement. Each participant is required to consider sequence of work when determining the degree of detail required."
This excerpt is a small example of the level of detail and complexity required to create a spatially coordinated construction model suitable for fabrication.
Information Provenance
"Establishing the provenance of building information immediately raises the specter of liability for the original authors of that information, particularly for design professionals, for whom professional liability may extend far beyond their responsible control of the information…e provenance of building information must be sufficiently clear and complete to permit anyone intending to use it to judge the reliability of it for themselves… the building industry as a whole is clearly moving toward a new business environment — supported by new forms of legal agreements — in which the burden of responsibility for relying on the building information is shifting… from the original author to the person using it."14
Copyright 2010 The Construction Users Roundtable. All rights reserved
Drawing Production
Shop, installation, and fabrication drawings are produced as extractions from the spatially coordinated BIM. Fully annotated and dimensioned paper sheet sets are produced and formally submitted with the digital model to the design team for review of compliance with design.
As-built deliverables and turnover documents
Building Information Modeling presents opportunities for digital document turnover packages far superior to traditional paper- based deliverables. When produced in an archival quality format such as the Construction Operations Building Information Exchange (COBIE), these packages offer the owner a higher assurance of the ability to retrieve usable data over time.
"The COBIE approach is to enter the data as it is created during design, construction, and commissioning (see Figure 1). Designers provide floor, space, and equipment layouts. Contractors provide make, model, and serial numbers of installed equipment. Much of the data provided by contractors comes directly from product manufacturers who can also participate in COBIE."
Design and Construction Summary
"The Power of Sixteen Concept theorizes that effort in the top 20% of an activity is 16times more important than the other 80%. In project terms, this means that, if you focus on improving up-front decisions, you can put yourself in the position of maintaining the advantage during production…"
14Construction Operations Building Information Exchange (COBIE)
by E. William East, PE, Ph.D http://www.wbdg.org/resources/cobie.php
15 Big BIM Little BIM (Finith Jernigan) ISBN: 978-0-9795699-9
Copyright 2010 The Construction Users Roundtable. All rights reserved
Focusing on the integration of design with spatial coordination and installation level detail before developing construction documents will yield highest and best outcomes on a project. Incomplete or inaccurate design models and deliverables produced for the sake of permitting and bid documents require additional effort before construction, which may exceed any perceived savings from competitive bidding.
5.0 Operations and Maintenance
Leveraging BIM beyond construction to assist stakeholders during the operation of facilities is probably the highest level of maturity in the application of intelligent models to date. Ultimate success and adoption depends heavily on the interoperability and development of software standards. The following considerations leverage the BIM value created in Project Pre-Planning and Design and Construction.
Depending on the size of your portfolio and your existing approach to operations of existing facilities, your strategy is likely to differ. If your portfolio is large, consider how this project fits into your enterprise-wide solution. If it is small, look to owner peers, BIM vendors, or your design and construction teams to become familiar with what others are doing.
The extent you use BIM in your operations and maintenance program is scalable. It is also likely to change rapidly as the use of software, along with its usability, continues to improve. Even if you are looking at a light commercial or simple office building, there is some value in considering BIM in your operations program. How much you receive from your design and construction teams will determine your value.
Consider the following list of questions to assist in forming an implementation strategy for using your BIM in facility operations and maintenance:
Copyright 2010 The Construction Users Roundtable. All rights reserved
How are you managing your systems now?
Do you want to incorporate BIM into your existing strategy?
Is this an opportunity to formulate a new strategy?
Is this a catalyst to review your existing technology, processes, and workflow?
How large is your portfolio of assets?
Are you in a position to use BIM during Operation and Maintenance of the project?
Owners who have the benefit of having intelligent models during the design and construction phase are positioned to use the model and (more importantly) the information it contains in the operation and maintenance phase of their facility. The level to which the information models are used during operations and maintenance phase is dependent upon the scope that was required during the project team assembly, the elements that were modeled, how well the model was kept current, your internal ability and willingness to embrace the technology required to access the information, and the ease of retrieval of data.
Current Facilities Management Strategy
Consider the way information is stored, retrieved, and used in your current process and determine if there are areas of benefit for a BIM-enabled system or process.
The four "levels" of integration of digital information
into facility management:
Tagging data with hypertext links (e.g., attaching Word, Excel, or PDF documents).
Customized graphical interface with specific data.
Information automatically transferring to or from the model and the FM system (one direction).
Information automatically transferring between the model and FM system (bi-directional).
Copyright 2010 The Construction Users Roundtable. All rights reserved
Structure your Requests for Proposals to identify all available data and information possible even if you do not plan to or cannot use the information today. For example, request electronic as-builts with as much information as possible. Chances are very high that you will want to use that information in the near future.
The lack of interoperability and industry-wide standards
make the third and fourth levels economically challenging. Currently facility owners develop customized software or use middleware to accomplish this transfer of information.
Information required – When considering the use of
digital facility management tools, the first question owners should ask is, "What are we trying to do?" Based on the answer, a facility manager can focus on determining which information is required to support facility management.
Accessing BIM data — Database management is a
critical aspect and must be planned for in your operations and maintenance strategy. One challenge facing early users is not having readily available access to all of the information they are collecting.
Target specific areas for BIM adoption — Most owners
who use BIM on their projects during design and construction have initially focused on space management and equipment tagging of major building systems (HVAC, electrical, etc.). Energy control is a logical next step for Facilities Management using BIM.
The following is a list of the primary areas facility managers may derive benefit from the digital information that a model might offer.
Space Management
Building Systems / Equipment
Energy Control / Monitoring
Copyright 2010 The Construction Users Roundtable. All rights reserved
Finishes and Materials
Linking BIM to Asset, Facility Management and Space
Management Programs
Developing a clear understanding of the necessary information interfaces is critical to successful implementation. Consider:
Which existing or new software programs do I want the information to connect?
How many people are likely to use the programs? Are adequate seat licenses available?
Will this have an impact on future RFPs?
Are there interoperability issues?
Are naming conventions between the packages supportive of easy understanding and exchange? (See Figure 2, below.)
Figure 2: Facility Numbering Convention
Copyright 2010 The Construction Users Roundtable. All rights reserved
Other uses of the information contained in your
BIM There are other possible ways that people have made use of their digital information models during the operation of their facilities. Some of these include:
Capturing lessons learned
Preplanning future projects
Regulatory, statutory, permitting, etc.
Remote tie to other locations geographically
Emergency Response Teams
Future of BIM and Business Information Management
Facility management information that pertains to the operation of your business is the last consideration. Perhaps this crosses the line from facility management into business management. Future discussions will include looking at a comprehensive enterprise wide system, connecting facility management systems into operations, production, inventories, materials handling, business planning, and other system types.
BIM and Facility Management Summary
Owner use of BIM for Facility management is currently an untapped well of opportunity. As adoption and industry acceptance improve, owners my find uses for the Information Model that provide high ongoing value. Improvements in data storage and retrieval methods linked with higher levels of interoperability may increase use. As a minimum owners should require data to be transferred at the closeout of construction in a format that will have lasting accessibility.
Copyright 2010 The Construction Users Roundtable. All rights reserved
6.0 References
American Institute of Architects (AIA): AIA E202 BIM
Protocol Exhibit
American Institute of Architects (AIA): AIA's Technology In
Architectural Practice Knowledge Community:
American Institute of Architects (AIA)
Integrated Project Delivery: A Guide
American Institute of Architects (AIA)
Resources for Integrated Project Delivery
Associated General Contractors of America (AGC)
AGC BIM Forum MEP Spatial Coordination Requirements
for Building Information Modeling
Associated General Contractors of America (AGC)
BIMForum
Associated General Contractors of America (AGC)
Contractors Guide to BIM
Arizona Revised Statutes §34-603
Big BIM Little BIM (Finith Jernigan) ISBN: 978-0-9795699-9
Copyright 2010 The Construction Users Roundtable. All rights reserved
BIM Handbook A Guide to Building Information Modeling
(Eastman, Teicholz, Sacks, and Liston) ISBN: 978-0-470-
18528-5
Building Information Modeling" "A Strategic
Implementation Guide" (Smith and Tardif) ISBN: 978-0-470-
25003-7
BuildingSMART Alliance
ConsensusDOCS
301 BIM Addendum
Construction Operations Building Information Exchange
(COBIE) By E. William East, PE, PhD
http://www.wbdg.org/resources/cobie.php
Construction Users Roundtable
WP 1003 – Construction Strategy: Optimizing the
Construction Process
Construction Users Roundtable
WP 1202 – Collaboration, Integrated Information and the
Project Life Cycle in Building Design, Construction and
Operation
McGraw Hill
2009 SmartMarket Report "The Business Value of BIM":
National Building Information Modeling Standard (NBIMS):
Copyright 2010 The Construction Users Roundtable. All rights reserved
Project Execution Planning Guide:
Sustainability of Digital Formats
U.S. General Services Administration
Building Information Modeling
Copyright 2010 The Construction Users Roundtable. All rights reserved
Construction Users Roundtable Publications
The purpose of developing Construction Users Roundtable (CURT) publications is to disseminate recommendations, guidelines, and reports developed by the Construction Users Roundtable. CURT is focused on improving the cost effectiveness of the U.S. construction industry. These publications have been developed from the point of view of owners or users of construction services. Efforts by all segments of the industry, however, are vital if major improvement is to be the result.
This publication is one of a series from committees or study teams addressing a problem area.
Findings and recommendations of The Construction Users Roundtable are included in publication series classified as White Papers (WP), Reports (R), or User Practices (UP). In addition to these classifications, CURT publications are numbered based on the category of the topic:
Category
Number Code
Constructability
Contractor Management
Interface Management
Workforce/Industrial Relations
Material Control
Work Planning and Scheduling
Technology/E-Sourcing
Special Projects
Examples:
A CURT White Paper on Reverse Auction
A CURT Report on Tripartite Initiatives
A CURT User Practice on Construction Safety in Contractor Prequalification
Available CURT Publications
White Papers
• WP 401 Confronting the Skilled Workforce Shortage
• WP 410 CURT – CWDC Joint Workforce Initiative
• WP 1003 Construction Strategy: Optimizing the Construction
• WP 1004A Construction Strategy: CURT's Path Toward LEAN
Project Delivery
• WP 1201 Guidelines on the Use of Reverse Auction Technology
• WP 1202 Collaboration, Integrated Information and the Project Life
Cycle in Building Design, Construction and Operation
• R 402 CURT Tripartite Initiative Executive Summary
• R 402A CURT Tripartite Study on Extended overtime on
Construction Projects
• R 402B Reducing Absenteeism Report
• R-402C Tripartite Initiative Report: Eliminating Work Disruptions
and Jurisdictional Disputes
• R405 CURT Tripartite Initiative Report: Project Stakeholder
Responsibilities
• R411 Building Comprehensive Labor Market Information
• R 807 CURT Owner Safety Blueprint
User Practices
• UP 101 Construction Measures: Key Performance Indicators
• UP 201 Construction Project Controls: Cost, Schedule, and Change
• UP 403 Construction Labor: Managing the Construction Workforce
• UP 601 Construction Purchasing: Capital Purchasing & Contracting
• UP 701 Construction Quality: Achieving Quality on Capital Projects
and Craft Worker Prequalification
• UP 801 Construction Safety: Contractor and Craft Worker
Prequalification
• UP 802 Construction Safety: The Owner's Role
• UP 803 Construction Safety: Pre-Bid and Bid Clarification Meetings
• UP 804 Construction Safety: Contract Terms and Conditions
• UP 805 Construction Safety: Monitoring Performance
• UP 806 Construction Safety: Improving Safety Programs
• UP 1001 Construction Strategy: Selecting Contracting Strategies
• UP 1002 Construction Strategy: Selecting the Right Contractor
• T 404 Construction Labor: Craft Employee Training Evaluation Tool
• T 808 Construction Safety: Owner Safety Blueprint Assessment Tool
Training Modules
• TM 809 Construction Owners' Safety Blueprint Training Module
Survey Summaries
• SS 406 CURT Tripartite Initiative: Workplace Attitudes Survey,
Summary of Results
• SS 407 CURT Owner Survey: Impact of Gulf Coast hurricanes on
Owner Projects, Summary of Results
Visit the CURT publications website,
for additional information and pricing.
4100 Executive Park Drive, Suite 210
Cincinnati, OH 45241-4023
Phone (513) 563-4131
Fax (513) 733-9551
Source: http://www.fmsystem.com.au/pdfs/CURT_BIM.pdf
Guide to Cementation Your practice is our inspiration.™ Guide to CementationClinical Guide Cementation in Dentistry Prosthodontic Procedure - All you need is Kerr Mechanical & Physical Properties Temporary Cementation Permanent Cementation Adhesive Cementation Review When to use our cements Author Biographies Your practice is our inspiration.™
Revista de Revistas Boletín El Dolor 46 (16): 52 - 54, 2007 Dr. Rodrigo Fernández R.* Efecto analgésico de vitamina E en el dolor dosis que está dentro del rango terapéutico usado en neuropático se produce por una disminución en humanos (2000-5000 U.I. = 2-5 gramos). la sensibilización a nivel central